In-Floor - Set Point 104°f but surface only 83°f ?
opaone
3 years ago
Featured Answer
Sort by:Oldest
Comments (40)
Elmer J Fudd
3 years agoopaone
3 years agoRelated Discussions
you only get to pick one...only one!
Comments (35)pupwhipped here...the OP of this thread. Wow, it is ALL really hard to choose isn't it?!? But, ya know, I feel a bit like a fool sometimes to be complaining about being saddled with this burden. Once when I was whining to a friend about how overwhelming it was to me to be remodeling the kitchen in my recently purchased lake home built in 1952, my friend replied, "Kathy, this should be such FUN. I would love and enjoy to the max this project you perceive as torture.....if only I could afford it." That kinda put it all in perspective. She will never get this chance, and here I am complaining about it all and not enjoying the process. But, you guys know it really is such a stress because you don't want to make a bad decision....and all this kitchen sh*t IS soooooooo expensive! Ohhhhhhhhhhh, woe is me. I do pontificate, but I will still say backsplash is going to be the end of me. Thanks for all the responses. I do think it helps to share our angst. I haven't done a tally yet, but maybe I will do that eventually to see which kitchen decision is the most difficult from our GW group perspective. But, as I mentioned before, let's all just be grateful that we are blessed to have these difficult decisions to make. Good kitchen remodel luck to us all.....and let us all be thankful for the opportunity....See MoreMud Set vs. Thin Set
Comments (6)I think this is a good explanation. If Bill is around he'll have a more specific answer for you. I have tiled counters and walls that aren't straight, so it wasn't just a backsplash issue for me. Mine is the cured mud with thinset application version. My glass tile backsplash in my laundry is as well, with an anti-fracture membrane. My floors are on a floated levelling layer of cement goop and anti-fracture membrane. If you have mud and a good tiler, you have a nice, smooth, level continuous surface. Always with tiling, the better the substrate the better the tile job. There are other ways to treat a wall which give perfectly good backsplashes, however. If you have traditionally wet set tiles they'll never ever come out. Ever. The only way to remove them is to break them, though I suppose, if you were patient, you could dig out the grout, then use wires to wiggle in and dig out the mud until you loosened a tile, or something like that. That's also where you'll get a crack in an earthquake because tiles don't bend. With the thin set, you can get cracks along the grout instead of right through the tiles. No one really does wet set anymore, however. Certainly not for a backsplash. I think mud sets may be thicker than "thin" sets, seeing as how those are thin, but that depends on how the wall is prepared. That's my experience, anyway. You'll have to talk to your tile setter to really know what's up....See MoreOne too many floor surfaces?
Comments (23)Williamsem: No, I am afraid I don't have any info on that tile. I am pretty sure it is original to the house, although I do not know that for certain. (It was the same height as the original wood floors, so I suspect it was never redone.) I assume you did see the better picture of it in the OP? (If you want a better picture, I can take one.) Breezy: Awww, shucks! Merci....See MoreHow To Make Toilet Less of a Focal Point???
Comments (104)I did try various looks for the curtains, lowered the pull backs, raised them, allowed them to just hang; the way they are now is was what looked okay to me. As the room evolves, these ones may get swapped out; for now they'll be fine. I also tried a heavier white curtain with white dots in the fabric which was too much as well as a valance that was totally hideous. Ohmygosh, the table is incredibly useful!!! I'm a huge fan of small, versatile pieces of furniture like tables and benches that can easily be moved around if need be, so this one was ideal. Many tables like this have a bottom shelf which I'm much happier without....See Moreformulaross20
3 years agoElmer J Fudd
3 years agolast modified: 3 years agoAustin Air Companie
3 years agomike_home
3 years agoopaone
3 years agolast modified: 3 years agoAustin Air Companie
3 years agoopaone
3 years agomtvhike
3 years agoopaone
3 years agommmm12COzone5
3 years agolast modified: 3 years agosktn77a
3 years agoElmer J Fudd
3 years agolast modified: 3 years agoElmer J Fudd
3 years agoAustin Air Companie
3 years agoBruce in Northern Virginia
3 years agoopaone
3 years agolast modified: 3 years agoopaone
3 years agoAustin Air Companie
3 years agoAustin Air Companie
3 years agoopaone
3 years agoopaone
3 years agolast modified: 3 years agoopaone
3 years agoopaone
3 years agomike_home
3 years agoAustin Air Companie
3 years agoopaone
3 years agolast modified: 3 years agoopaone
3 years agolast modified: 3 years agoAustin Air Companie
3 years agommmm12COzone5
3 years agoBruce in Northern Virginia
3 years agoAustin Air Companie
3 years agolast modified: 3 years agofsq4cw
3 years agoopaone
3 years agolast modified: 3 years agoElmer J Fudd
3 years agolast modified: 3 years agommmm12COzone5
3 years agoopaone
3 years ago
Related Stories
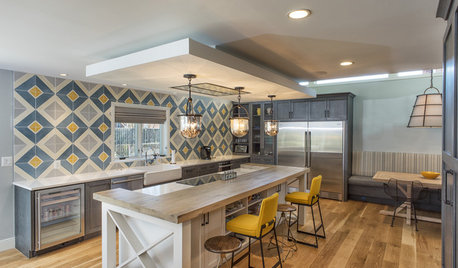
KITCHEN DESIGNKitchen of the Week: Tile Sets the Tone in a Modern Farmhouse Kitchen
A boldly graphic wall and soft blue cabinets create a colorful focal point in this spacious new Washington, D.C.-area kitchen
Full Story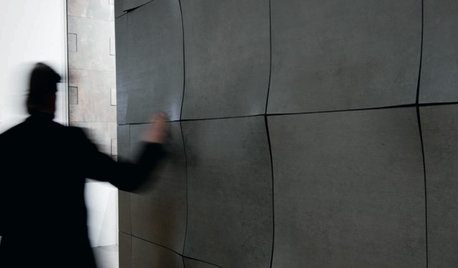
MATERIALSShape Up Your Surfaces With New Tile Textures and Forms
Take your walls and floors to a different dimension with innovative sculptural tiles, as shown at the 2013 Coverings expo
Full Story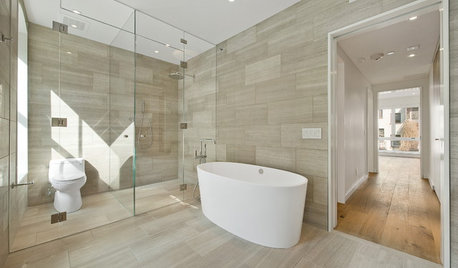
REMODELING GUIDESTransition Time: How to Connect Tile and Hardwood Floors
Plan ahead to prevent unsightly or unsafe transitions between floor surfaces. Here's what you need to know
Full Story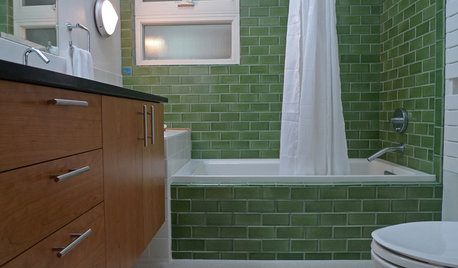
BATHROOM DESIGNBathroom Surfaces: Ceramic Tile Pros and Cons
Learn the facts on this popular material for bathroom walls and floors, including costs and maintenance needs, before you commit
Full Story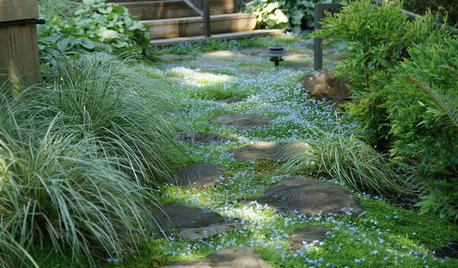
LANDSCAPE DESIGNHow to Pick the Right Floor for Your Garden Room
Crunch the facts on gravel, flagstone, brick, tile and more with our mini guide to outdoor flooring surfaces
Full Story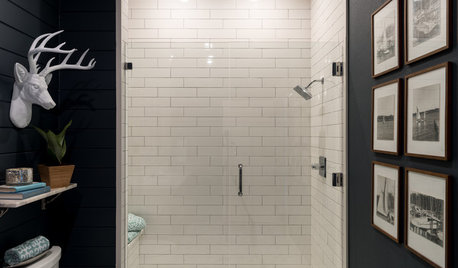
BATHROOM DESIGNA Rustic Setting and a Paint Mistake Create Drama in the Bathroom
Near-black walls, wood features and elegant surfaces personalize this lake house bathroom
Full Story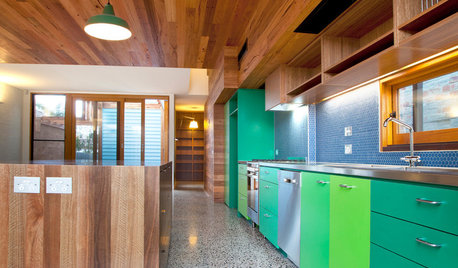
FLOORSMake Your Floors Terrific With Terrazzo
Durable, sanitary and unique, this bespeckled surface is a winner for floors, walls, countertops and sinks
Full Story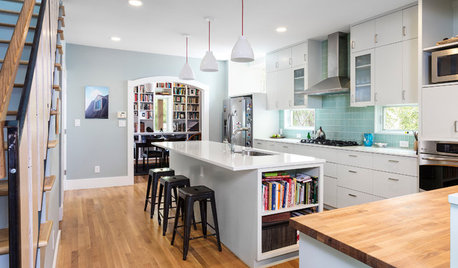
MOST POPULAR6 Kitchen Flooring Materials to Boost Your Cooking Comfort
Give your joints a break while you're standing at the stove, with these resilient and beautiful materials for kitchen floors
Full Story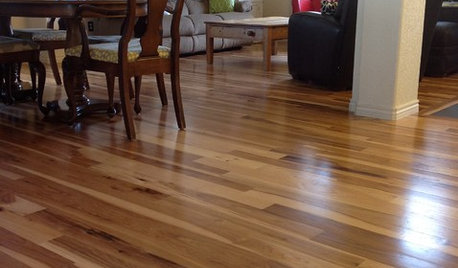
MATERIALSWhat to Ask Before Choosing a Hardwood Floor
We give you the details on cost, installation, wood varieties and more to help you pick the right hardwood flooring
Full Story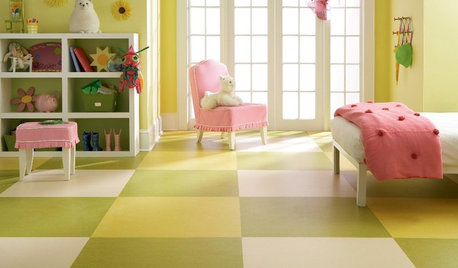
REMODELING GUIDESThe Case for Linoleum and Vinyl Floors
Have pets, kids and a tight budget? Easy-care resilient floors may be the choice for you
Full Story
mmmm12COzone5