Glued Down Engineered Floor Creaks/Pops/Hollow Places
kpyeatt
3 years ago
Featured Answer
Sort by:Oldest
Comments (16)
SJ McCarthy
3 years agokpyeatt
3 years agoRelated Discussions
Can you glue down a click-n-lock engineered wood floor?
Comments (7)Although not in any way 'necessary' due to the self-interlocking nature of the click system. (In fact that was why it was developed) However, there is absolutely no reason I can ascertain why the click systems can't also be nailed or glued down to the substrate if desired just like an engineered T+G system if one likes the totally solid feel underfoot. Solid wood flooring is nailed or glued down to try to limit its thermal movement. Engineered flooring is in fact cross plyed layers of wood anyway which are all glued to each other to enhance stability. So fixing it again down to the substrate rather than installing in a floating way would have no adverse effects. It would be in no way any messier (as suggested by user floorguy) than any other system ! It is all in the skill of the installer. Not all DIYers are hacks after all. Infact they can do a better/neater job than a pro as they are not conscience of the time to finish and move on to the next job. But like i said, it rather goes against the point of the system BUT can be done if required. Achitect...See Morenew laminate flooring creaking - mysterious!
Comments (9)I know how annoying it is when you can't even have a conversation because the noise of the floor is great. We have the same problem with a locking type of flooring (Preverco engineered hardwood) and I had assumed that because it was locking and no glue was used, that makes it creak more (wood rubbing on wood). In our case, there are issues with the concrete subfloor level AND with too small of expansion gaps, so it might not be the floor's fault. But I did want to point out that you won't necessarily avoid it with something that locks....See MoreSolid wood floor glued down on concrete: hollow spots
Comments (111)They will say that it is a site related issue - that is what they are saying - "CLIMATE" - which they may claim they have no control over, only the homeowner is responsible for that. Wood has predictable behavior. They should, since they are professional installers, have all of the documentation regarding the ambient air conditions before and during installation as well as the rh/calcium chloride test results (whichever one they performed and you paid for - hopefully) and ph of the concrete - most professionals include that documentation or report with the final invoice to the end user and kept as long as the floor is under the manufacturer's warranty. Technically, if you wrote 2 checks, it is your responsibility to make sure that was done....See MoreGlued down Engineered Flooring
Comments (37)There was zero dust in my house after undercutting my fireplace brick and grinding the slab. The installer had two gigantic hepa vacuums attached to each other and to his grinder. I was home during the install and didn't see any dust flying around at all, and there was none left when it was all over either. My slab looked to be in incredible condition compared to most that I've seen and it still needed a good deal of prep work. The installer went over every inch of it with a straight edge and marked all the high and low spots and there were some in every room. All of those areas were addressed before installing the wood. Additionally, the entire floor was roughed up with a grinder before any work started. If your installers showed up at your house and started gluing down wood the first day without checking everything first, that's a problem. From your manufacture's website for glue down: All Concrete sub-floors must be dry, smooth (level with 3/16” in a 10 foot Radius – 1/8” in 6”) and free of structural defects. Hand scrape or sand with a 20 grit #3-1/2 open face paper to remove loose, flaky concrete. Grind high spots in concrete and fill low spots with a Portland based leveling compound (min. 3,000 psi)....See Morekpyeatt
3 years agokpyeatt
3 years agokpyeatt
3 years agoSJ McCarthy
3 years agokpyeatt
3 years agoSJ McCarthy
3 years agokpyeatt
3 years agokpyeatt
3 years agoG & S Floor Service
3 years agokpyeatt
3 years agoG & S Floor Service
3 years agolast modified: 3 years agokpyeatt
3 years agoSJ McCarthy
3 years ago
Related Stories
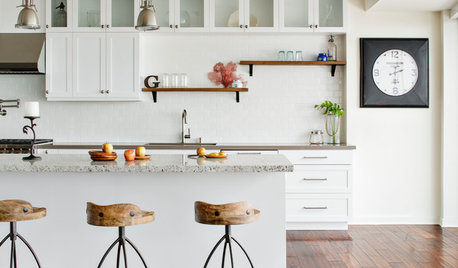
REMODELING GUIDESWhat to Know About Engineered Wood Floors
Engineered wood flooring offers classic looks and durability. It can work with a range of subfloors, including concrete
Full Story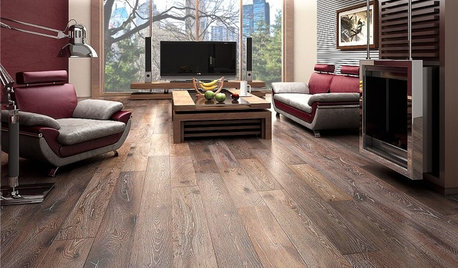
REMODELING GUIDESWhen to Use Engineered Wood Floors
See why an engineered wood floor could be your best choice (and no one will know but you)
Full Story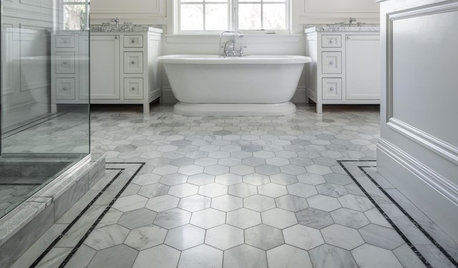
TILEWhy Bathroom Floors Need to Move
Want to prevent popped-up tiles and unsightly cracks? Get a grip on the principles of expansion and contraction
Full Story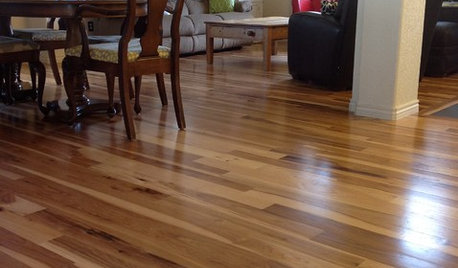
MATERIALSWhat to Ask Before Choosing a Hardwood Floor
We give you the details on cost, installation, wood varieties and more to help you pick the right hardwood flooring
Full Story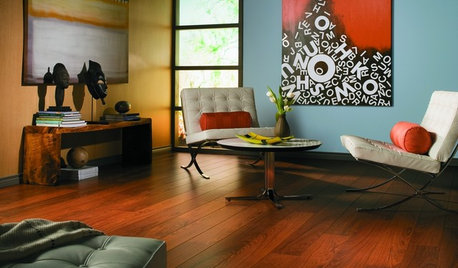
REMODELING GUIDESLaminate Floors: Get the Look of Wood (and More) for Less
See what goes into laminate flooring and why you just might want to choose it
Full Story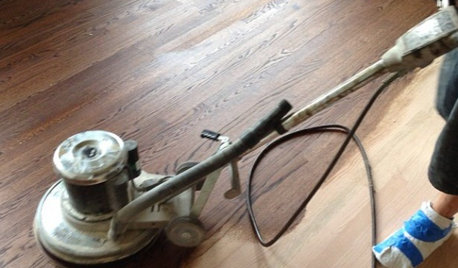
GREAT HOME PROJECTSWhat to Know Before Refinishing Your Floors
Learn costs and other important details about renewing a hardwood floor — and the one mistake you should avoid
Full Story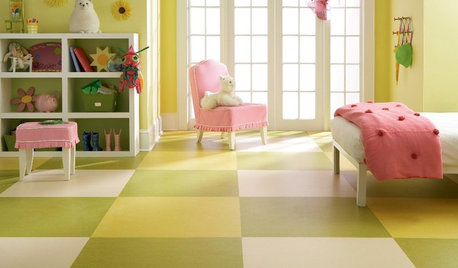
REMODELING GUIDESThe Case for Linoleum and Vinyl Floors
Have pets, kids and a tight budget? Easy-care resilient floors may be the choice for you
Full Story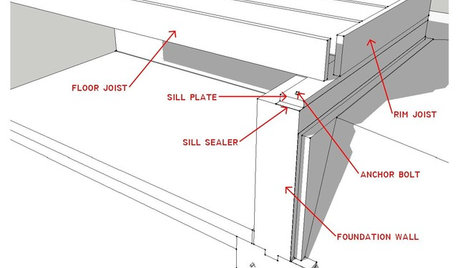
KNOW YOUR HOUSEKnow Your House: What Makes Up a Floor Structure
Avoid cracks, squeaks and defects in your home's flooring by understanding the components — diagrams included
Full Story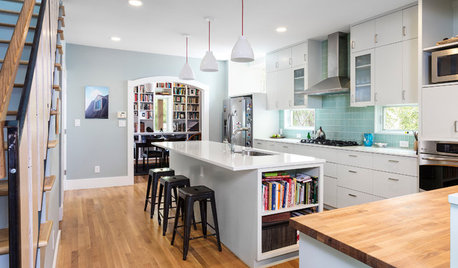
MOST POPULAR6 Kitchen Flooring Materials to Boost Your Cooking Comfort
Give your joints a break while you're standing at the stove, with these resilient and beautiful materials for kitchen floors
Full Story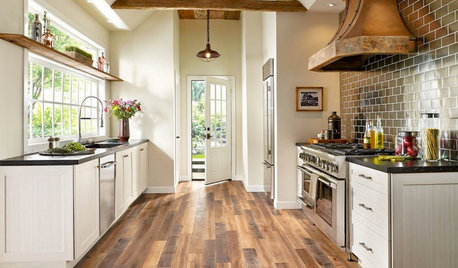
MOST POPULARPros and Cons of 5 Popular Kitchen Flooring Materials
Which kitchen flooring is right for you? An expert gives us the rundown
Full Story
millworkman