Help with Crowning & Gapping Reclaimed Oak Floors
tahoeshack
7 years ago
Featured Answer
Sort by:Oldest
Comments (7)
Related Discussions
Getting reclaimed wood floors from new floors?
Comments (9)I don't think you'll find any stain or staining technique that will give you a wide light to dark finish variation. As I understand it, that look comes from the wood, not the stain. Like you, we have 4" white oak "mill run" (what our GC called it; I suspect it is the same as character grade) flooring, and we chose to go with MinWax "Provincial". There isn't a stark light-to-dark difference between the boards, but we do have a lot of grain variation and plenty of knot holes. Good luck with your finishing!...See MoreReclaiming Hardwood Red Oak Floors..help!
Comments (1)Did you post this in another forum? I could swear I answered it....See MoreHELP...would love this European White Oak coloring in vinyl flooring
Comments (14)The surface must be SMOOTH AND FLAT. The tiles must be COVERED in cement. To do that, they must be sanded, primed and then COATED in concrete. The cost is roughly the same as removing them (which is ALWAYS the right thing to do). And if you coat them in cement, you will RAISE THE FLOOR by another 1/4" - 1/2" + the new floor. Your concerns are correct. The coating the tiles is *possible but not the best way to go about it (but it is *easier on the guys)....See MoreCracks and Gaps Around Crown Molding
Comments (7)You’re not going to be able to stop the wood drying out and there are other components in the house that rely on a standard range of humidity. Turn your humidifier back on. The movement that your builder is referring to is mainly in the framing. Wood moves with changes in moisture content. It sounds like your builder has planned for it and is intending to remediate issues. Just live with the cracks for the time being....See Moretahoeshack
7 years agoUser
7 years agoSelect Hardwood Floor Co.
7 years ago
Related Stories
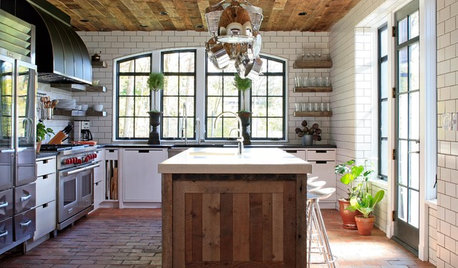
KITCHEN DESIGNWhat to Know About Using Reclaimed Wood in the Kitchen
One-of-a-kind lumber warms a room and adds age and interest
Full Story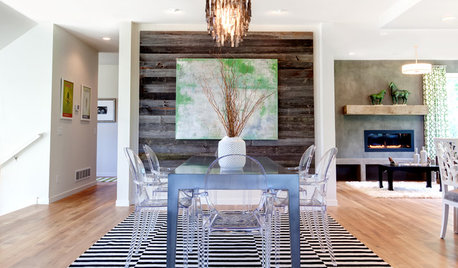
GREAT HOME PROJECTSWhat to Know About Adding a Reclaimed-Wood Wall
Here’s advice on where to put it, how to find and select wood, what it might cost and how to get it done
Full Story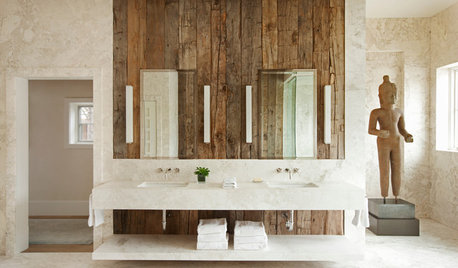
DECORATING GUIDESHow to Bring the Beauty of Reclaimed Wood to the Bath
Beautiful salvaged wood adds warmth and texture to a bathroom. Here's how to get the look right
Full Story
WINDOWSDiamond Muntins Help Windows Look Sharp
As the real deal or a decorative grille, diamond window muntins show attention to detail and add traditional flair
Full Story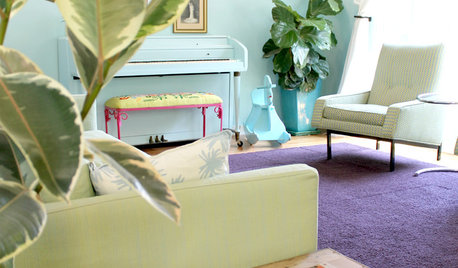
HOUZZ TOURSMy Houzz: Saturated Colors Help a 1920s Fixer-Upper Flourish
Bright paint and cheerful patterns give this Spanish-style Los Angeles home a thriving new personality
Full Story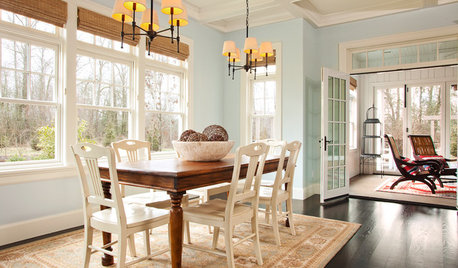
COLORPick-a-Paint Help: How to Create a Whole-House Color Palette
Don't be daunted. With these strategies, building a cohesive palette for your entire home is less difficult than it seems
Full Story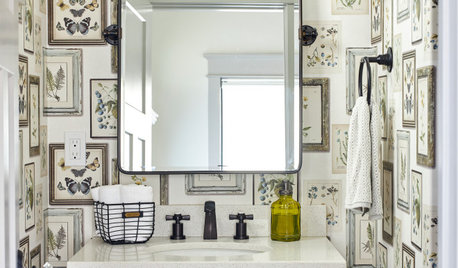
BATHROOM DESIGNKey Measurements to Help You Design a Powder Room
Clearances, codes and coordination are critical in small spaces such as a powder room. Here’s what you should know
Full Story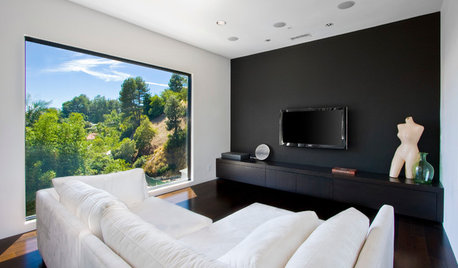
DECORATING GUIDESGot a Problem? 5 Design Trends That Could Help
These popular looks can help you hide your TV, find a fresh tile style and more
Full Story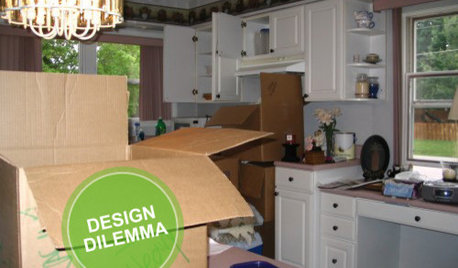
KITCHEN DESIGNDesign Dilemma: My Kitchen Needs Help!
See how you can update a kitchen with new countertops, light fixtures, paint and hardware
Full Story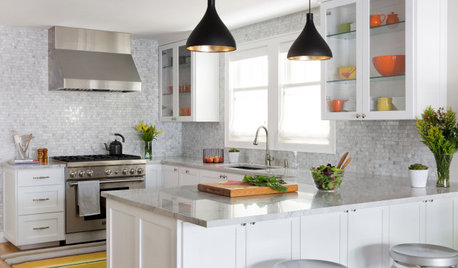
KITCHEN DESIGNKey Measurements to Help You Design Your Kitchen
Get the ideal kitchen setup by understanding spatial relationships, building dimensions and work zones
Full Story
User