Newly installed solid Hardwoods started making popping noises
browniebear
7 years ago
last modified: 7 years ago
Featured Answer
Sort by:Oldest
Comments (44)
millworkman
7 years agoCancork Floor Inc.
7 years agoRelated Discussions
Using Floor Muffler on 3/4 solid hardwood on plywood subfloor
Comments (9)I think the key word is "floating". This isn't a floating floor, it's a naildown. I don't believe it's going to be nearly as effective in a naildown situation, as most of the noise that is "muffled" in a floating situation is from the fact that there isn't good solid contact with the subflooring, as in nailed down. WHen there is good solid contact with a subfloor, the majority of the noise produced is from the reflective (rather than absorbtive) nature of the hardwood surface itself. Sound just echoes more into the air from a hardwood floor than it does from a sound absorbtive carpet floor. No amount of underlayment is going to alter the nature of the sound echo produced because the flooring is a hard floor product and not a textile based flooring product. It may be possible that installing a manufacture approved for naildown installation sound barrier can help with some of the percussive sound transmission from floor to floor, but it'll never be as quiet downstairs as if carpet on padding was the second floor material. And, you'll still get sound echoes upstairs that travel through the walls and open areas, simply because the wood surface reflects sound. You can't alter the basic nature of a hardwood floor. You can use rugs and additional soft furnishings to moderate the sound absorbtive properties and mitigate some of that reflectivity, but you'd have to practically cover all of the rooms wall to wall with rugs to make it be as quiet as carpet could be....See MoreNewly finished hardwood floors scratching so easy
Comments (19)We had the same problem with a dark stain over white oak. Contracter used Bona stain, and 3 coats of water based satin finish. Each dried at least 12 hours between coats. Our floors were very hard previously in the “golden oak” (natural) color but had yellowed and we didnt like the color. Now they scratch SO easily, as in drop a spoon and it scratches and dents the floor. We don’t wear shoes in the house either. Does not seem right. All the scratches 1 month later seem random, not from furniture, which is all on felt pads. What went wrong here?? I feel like I’m walking on eggshells....See MoreLarge Gaps Along Length of Hardwood Installed Just Months Ago
Comments (31)@bry911 I was reading through the comments so I could gather my thoughts for the flooring guy when I came across an old comment of yours that is incredibly helpful. Why did you add an essay to an old comment and not just post a new one? I'm not sure I ever would have seen it and it's very good information. Explains the longitudinal movement. I was stumped by that one. FYI, never said plain sawn lumber is the most stable, just thought it was important to the discussion. And I'm pretty sure we have agreed on wood movement the entire time. Also, not sure where you got the floor is bouncing from. It just makes a cracking sound once in a while. As for the floor, it's not something to get upset about, just a floor and can be fixed thanks to all the feedback I received. Your new info is amazing. Exactly what I was looking for earlier. Wood moves radially, tangentially, and longitudinally. Flat (plain) sawn lumber has the most widely varying grain pattern and therefore moves in the most directions. You appear to be asking why your gaps are happening at the end (longitudinal movement) rather than across the width. Which is a fair question, the most obvious answers to that question are poor layering of your core material, or that it isn't and you are just noticing it more on the ends of long boards and not noticing the gaps on the width as there are more of them. In essence, plywood gains dimensional stability by coupling tangential movement to longitudinal movement. Since longitudinal movement is much less than tangential movement (trees swell fatter with water rather than taller), this increases dimensional stability by limiting the amount the wood can swell without breaking the adhesive bond (that is why really thick face layers can be bad as the force of the movement overcomes the bond). In good plywood the grain is rotated many directions and so the wood has longitudinal resistance in all directions. However, poor plywood can actually increase longitudinal movement if most of the core layers are between 60° and 120° of the face layer you will see an increase in length shrinkage and a decrease in width shrinkage. Modern plywoods often use some composite core but those cores have the same quality issues. MDF is usually very dimensionally stable, while any of the chipboards can suffer from quality control issues. All of this means that the face layer and its quality are at the mercy of the core layers and their quality, which is what Tatt's said originally. ------- Of course, it can be the movement of the subfloor too, but a hardwood installer shouldn't be stumped by that. If your floor is bouncing a lot as you walk on it, then the floor is going to move, but your installer should have noticed that....See MoreNewly Installed Rigid Vinyl Plank Flooring Makes Crackle Sound?
Comments (95)I hear or notice the noise way less now, but still hear it from time to time when walking over an area for the first time. We have a couple of seams that have a small gap forming. As others have pointed out and i have come to learn, the problems that we have with the floors are caused by the unevern (not flat) subfloor. So, from that perspective, i cant blame flooret. However, most people that are buying these vinyl floors are doing so for the advertised ”value” and installing them in extisting homes. When you consider the time and expense to make old subfloors PERFECTLY flat, they are no longer a good value. That is my biggest complaint at this point; they drastically under communicate the amount of time and money required to achieve the desired outcome. To those of you who installed these Flooret floors, im sorry and hang in there. The noise and /or your attention to it will improve greatly over time....See Morebrowniebear
7 years agoUptown Floors
7 years agolast modified: 7 years agobrowniebear
7 years agorjs5134
7 years agoCarpet One Columbia
7 years agobrowniebear
7 years agobrowniebear
7 years agoCancork Floor Inc.
7 years agobrowniebear
7 years agoglennsfc
7 years agobrowniebear
7 years agoNancy
7 years agoUser
7 years agobrowniebear
7 years agoUser
7 years agolast modified: 7 years agobrowniebear
7 years agoglennsfc
7 years agobrowniebear
7 years agoUser
7 years agoUser
7 years agobrowniebear
7 years agolast modified: 7 years agobrowniebear
7 years agoNancy
7 years agoCancork Floor Inc.
7 years agobrowniebear
7 years agoULTIMATE HARDWOOD LTD
7 years agoCancork Floor Inc.
7 years agobrowniebear
7 years agoULTIMATE HARDWOOD LTD
7 years agoCancork Floor Inc.
7 years agobrowniebear
7 years agoULTIMATE HARDWOOD LTD
7 years agomjwkr2000
7 years agobrowniebear
7 years agoCancork Floor Inc.
7 years agomjwkr2000
7 years agobrowniebear
7 years agoglennsfc
7 years agobrowniebear
7 years agolast modified: 7 years agoCancork Floor Inc.
7 years agobrowniebear
7 years agolast modified: 7 years ago
Related Stories
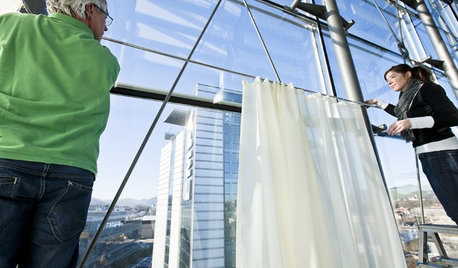
HOME OFFICESQuiet, Please! How to Cut Noise Pollution at Home
Leaf blowers, trucks or noisy neighbors driving you berserk? These sound-reduction strategies can help you hush things up
Full Story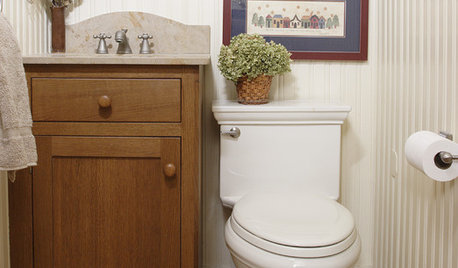
HOUSEKEEPINGWhat's That Sound? 9 Home Noises and How to Fix Them
Bumps and thumps might be driving you crazy, but they also might mean big trouble. We give you the lowdown and which pro to call for help
Full Story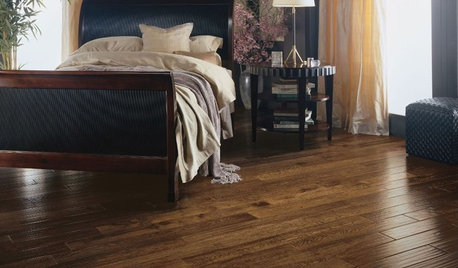
REMODELING GUIDESYour Floor: An Introduction to Solid-Plank Wood Floors
Get the Pros and Cons of Oak, Ash, Pine, Maple and Solid Bamboo
Full Story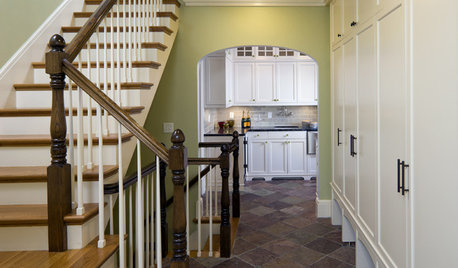
TILE6 Questions to Answer Before You Install Tile Flooring
Considering these things before tackling your floors can get you a better result
Full Story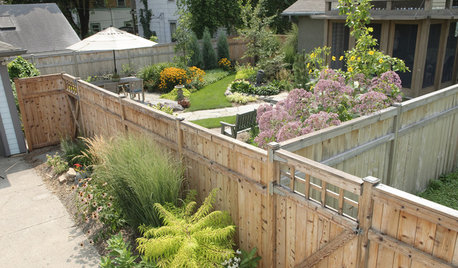
FENCES AND GATESHow to Install a Wood Fence
Gain privacy and separate areas with one of the most economical fencing choices: stained, painted or untreated wood
Full Story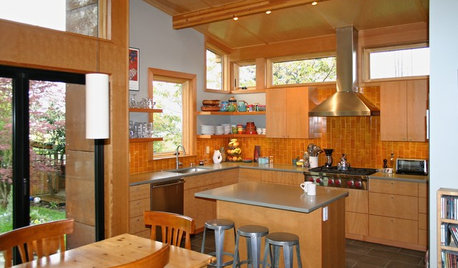
CONTRACTOR TIPS10 Things to Discuss With Your Contractor Before Work Starts
Have a meeting a week before hammers and shovels fly to make sure everyone’s on the same page
Full Story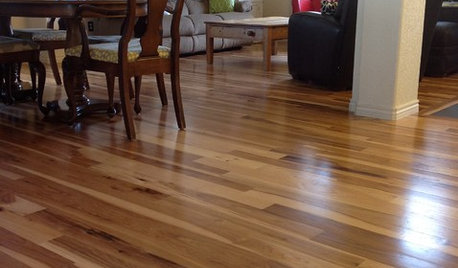
MATERIALSWhat to Ask Before Choosing a Hardwood Floor
We give you the details on cost, installation, wood varieties and more to help you pick the right hardwood flooring
Full Story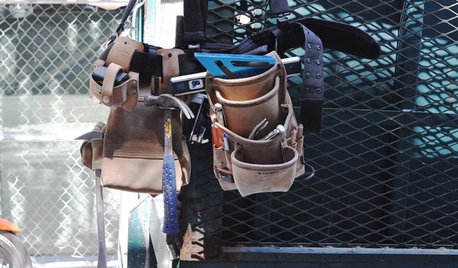
MOST POPULAR10 Things to Ask Your Contractor Before You Start Your Project
Ask these questions before signing with a contractor for better communication and fewer surprises along the way
Full Story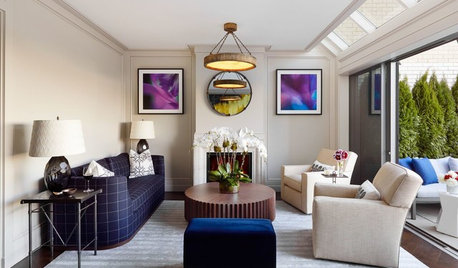
DECORATING GUIDESDecorating 101: How to Start a Decorating Project
Before you grab that first paint chip, figure out your needs, your decorating style and what to get rid of
Full Story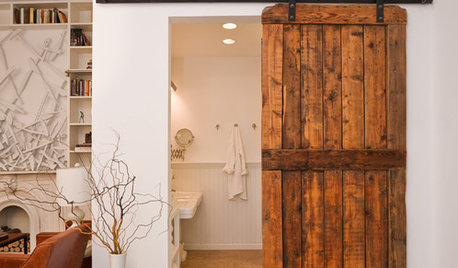
DOORS5 Questions to Ask Before Installing a Barn Door
Find out whether that barn door you love is the right solution for your space
Full Story
Cancork Floor Inc.