Load bearing beam
Emily Duffy
6 years ago
Featured Answer
Sort by:Oldest
Comments (41)
Related Discussions
Pricing on new load bearing wall beams
Comments (1)If your project has been calc'd out by your engineer and has the various sizes, make a list and present them to local suppliers. They will give you free quotes. If you dont have them spec'd, you will have to eventually, so maybe get a takeoff from your engineer....See MoreInstalling Pendants Around Load Bearing Beam?
Comments (4)Many pendant lights are available that are suspended by thin wire and can have the electrical connection off center from the hangar. You can then have a box installed adjacent to the beam and run the electrical wire there....See MoreTwo columns and a beam to support load bearing beam?oun
Comments (6)You need a structural engineer. Posts need footings. You’ll need to dig footings. Steel is stronger than glue lam, and smaller. It will not need intermediate support if designed correctly. Steel is always the answer. Along with a work crew that has experience with it. NOT DIYable. Structural work is like racing. How much you want it to be invisible depends on how much money you have. How fast do you want to go? Pony it up. A 300K level remodel is going to bleed it at every opportunity. This is where you need the experienced architect and GC and let them do their jobs....See Moreload bearing beam COST
Comments (14)What Jeffrey and Joe said, You figure the flitch plate will cost you $300-400... the microlam standard sizes are 7¼”, 9¼ so most likely you have to get 9 1/4" and rip to size unless you can find in that size... in any case 9 1/4" microlam will run you about $8 per foot so it will be $130-150 per beam so let's say $1,000 total + Carriage bolts, nuts and washers about 16-18 of each let say $5 per set lets say $100 give or take The rest is labor lets say another $1500-2000 roughly speaking put the beam together, and basic prep to put the beam up. Of course, the cost could increase depending on what needed to be done to put the beam in place. i.e if this a flush-mount install, in that case, the existing joists over a 17' span have to be cut to insert the beam, have to get and install beam hangers, etc so worst-case scenario figure 3k give or take... Whoever gave you 10k is a ridiculous price, for that you can get the whole house framed....See MoreJoseph Corlett, LLC
6 years agoEmily Duffy
6 years agoJoseph Corlett, LLC
6 years agogallagk
6 years agoUser
6 years agomillworkman
6 years agoWindows on Washington Ltd
6 years agoDenita
6 years agoJoseph Corlett, LLC
6 years agolast modified: 6 years agoDenita
6 years agolast modified: 6 years agoWindows on Washington Ltd
6 years agolast modified: 6 years agoJoseph Corlett, LLC
6 years agoSombreuil
6 years agoWindows on Washington Ltd
6 years agokudzu9
6 years agoJoseph Corlett, LLC
6 years agoWindows on Washington Ltd
6 years agolast modified: 6 years agoJoseph Corlett, LLC
6 years agodaisychain Zn3b
6 years agoksc36
6 years agoHelen
6 years agoksc36
6 years agoWindows on Washington Ltd
6 years agokudzu9
6 years agolast modified: 6 years agoHelen
6 years agolast modified: 6 years agoksc36
6 years agokudzu9
6 years agolast modified: 6 years agoHelen
6 years agolast modified: 6 years agodan1888
6 years agocatinthehat
6 years agoJoseph Corlett, LLC
6 years agojmm1837
6 years agocatinthehat
6 years agolast modified: 6 years agoksc36
6 years agocatinthehat
6 years agojmm1837
6 years agoJeff G
6 years agoMark Bischak, Architect
6 years ago
Related Stories
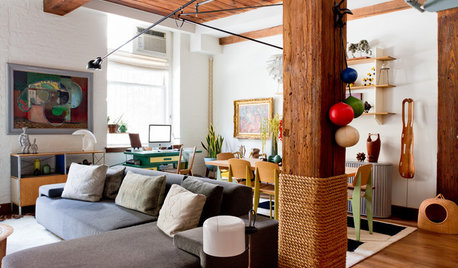
ARCHITECTURE21 Creative Ways With Load-Bearing Columns
Turn that structural necessity into a design asset by adding storage, creating zones and much more
Full Story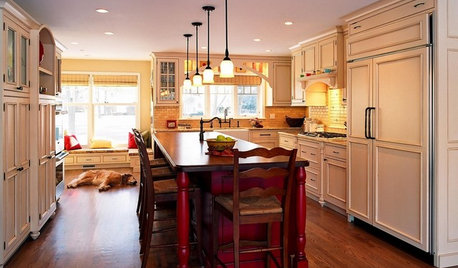
REMODELING GUIDESHouse Planning: When You Want to Open Up a Space
With a pro's help, you may be able remove a load-bearing wall to turn two small rooms into one bigger one
Full Story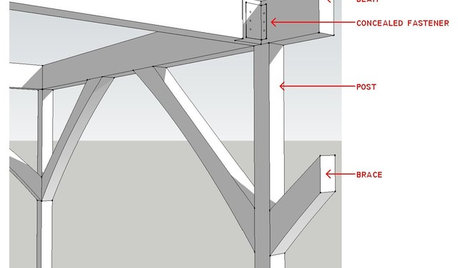
REMODELING GUIDESKnow Your House: Post and Beam Construction Basics
Learn about this simple, direct and elegant type of wood home construction that allows for generous personal expression
Full Story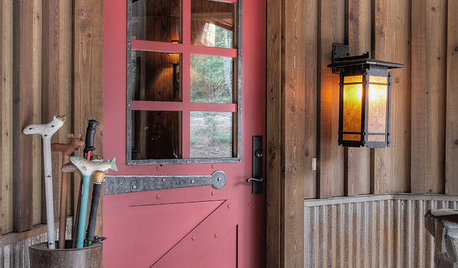
DESIGN DICTIONARYStrap Hinge
This strip may be narrow, but the weight it bears can be substantial
Full Story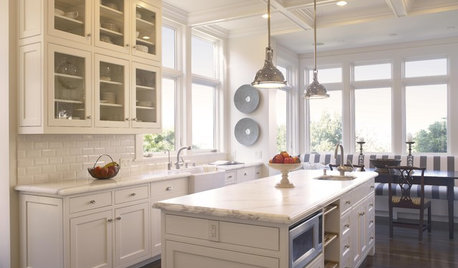
DESIGN DICTIONARYCoffered Ceiling
Sturdy does it, with beams and panels that evoke old-world artisanship and charm
Full Story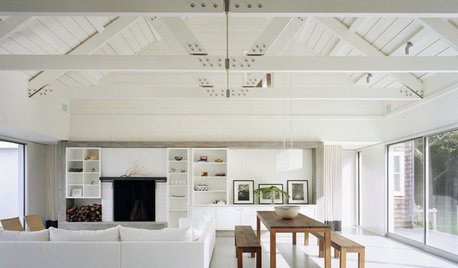
REMODELING GUIDESSupporting Act: Exposed Wood Trusses in Design
What's under a pitched roof? Beautiful beams, triangular shapes and rhythm of form
Full Story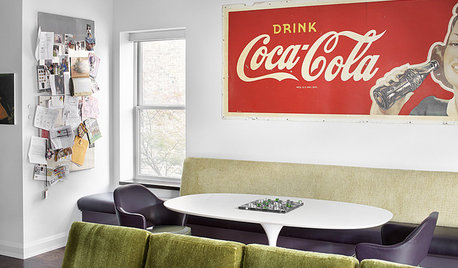
VINTAGE STYLEAmerican Icons: Coca-Cola Classic
Vintage items bearing the soda company's iconic red and white graphics are an ongoing hit in contemporary and modern interiors
Full Story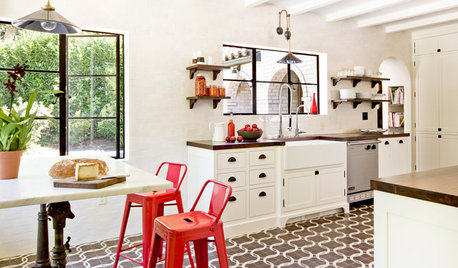
REMODELING GUIDESWhat to Know Before You Tear Down That Wall
Great Home Projects: Opening up a room? Learn who to hire, what it’ll cost and how long it will take
Full Story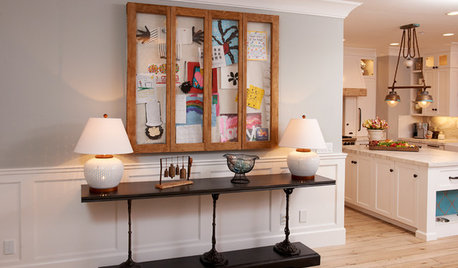
DECORATING GUIDESEdit Keepsakes With Confidence — What to Let Go and What to Keep
If mementos are weighing you down more than bringing you joy, here's how to lighten your load with no regrets
Full Story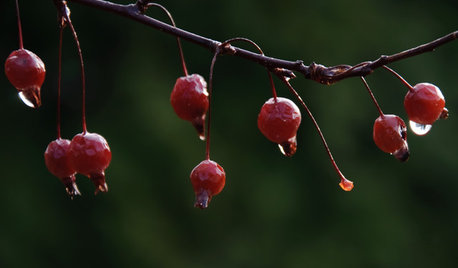
GARDENING FOR BIRDSFeed the Birds: 6 Plants for Abundant Winter Berries
Be kind to your fair feathered friends during lean food times by planting a shrub or tree loaded with nutritious snacks
Full Story
User