cost-effective home dimensions
bulldog09
15 years ago
Featured Answer
Sort by:Oldest
Comments (13)
Ron Natalie
15 years agoRelated Discussions
More cost effective way to run grow lights
Comments (6)Am in the amrket for grow lights in southern Ontario, can someone that knows about these, please point me in the right direction as to what to get, where from and any other info needed to get me going? Canadian tire, wal-mart or HD? I am after a setup like this: http://www.flippygirl.com/growlights.html...See MoreSuggestions for cost effective stone?
Comments (7)Thanks for the input. Gopintos, your house is looking wonderful - enjoy the process! Sweeby, thanks for your thoughts, that's exactly what I did today! Saw the product mentioned above by highjumpgirl and then saw some other natural stones. The stones quarried in my state are less expensive and may be an option based on what I saw. Seems like stone is at least worth considering to see if it fits with our house design and budget. Thanks....See MoreNeed ideas on how to cost effectively update a pool house
Comments (2)I will be renting it to a family member and they would have access to the kitchen in the main home. Just looking for ideas to spruce it up. @User...See Morewhich is the most cost effective roof style???
Comments (10)Not sure how you can't have a gutter on any side of a roof where it's needed. It's probably not bad luck, just misunderstanding. If you like Colonial and Cape Cod styles, then a hip roof is probably not going to lend to those styles. But, whether it's hip or a simple gable is a minor difference of cost, if any, in relation to the entire project. There are many other things which will take a bigger bite out of the construction cost, like not using an 8:12 pitch. And regarding your porch-under-the-gable question, do the math. For a 50'-8" width at 8:12, the height of the ridge (peak of roof) will be around a 16' tall space in the attic, so you'll have enough room for a 2nd story and depending it may seem out of proportion compared to the 1st story....See Morebulldog09
15 years agooruboris
15 years agonc_lawn_nut
15 years agomightyanvil
15 years agonc_lawn_nut
15 years agomightyanvil
15 years agomightyanvil
15 years agomissleah
15 years agobulldog09
15 years agomissleah
15 years agobulldog09
15 years ago
Related Stories
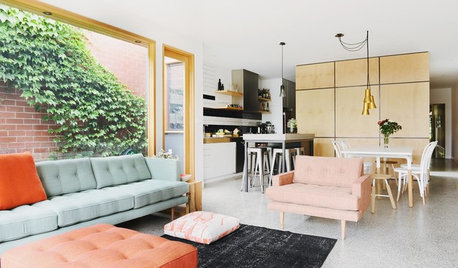
CONTEMPORARY HOMESHouzz Tour: Plywood Pod Adds a New Dimension to Living Spaces
Designers redo the back of a house for a better indoor-outdoor connection and install a clever structure for storage, function and flow
Full Story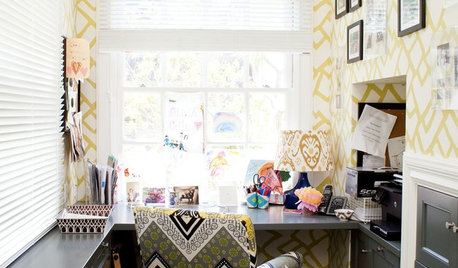
HOME OFFICESRoom of the Day: Home Office Makes the Most of Awkward Dimensions
Smart built-ins, natural light, strong color contrast and personal touches create a functional and stylish workspace
Full Story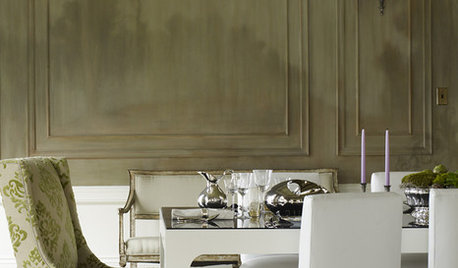
DECORATING GUIDESGive Your Walls an Architectural Dimension
Make a room special with the texture of wainscoting, panels, shiplap and more
Full Story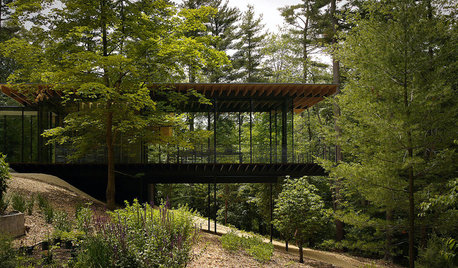
ARCHITECTUREDesign Workshop: The Intriguing Effects of Exposed Framing
Reveal the structure of your home for interesting design opportunities and eye-catching visual effects
Full Story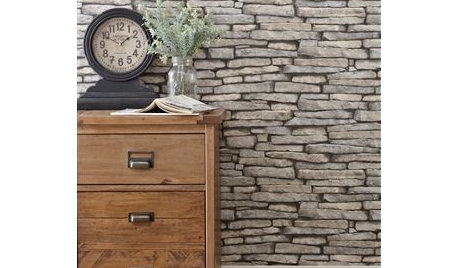
PRODUCT PICKSGuest Picks: Get in Touch With Textured-Effect Wallpapers
Mimic the look of fancy paneling, stacked stone or funky scrap wood with new wallpaper patterns on a trompe l'oeil roll
Full Story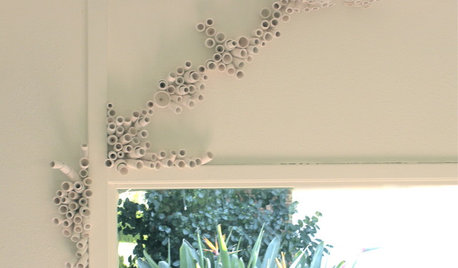
ARTChoose Art With a Third Dimension
Make a wall stand out with 3-D art of ceramic, wood, metal and cardboard
Full Story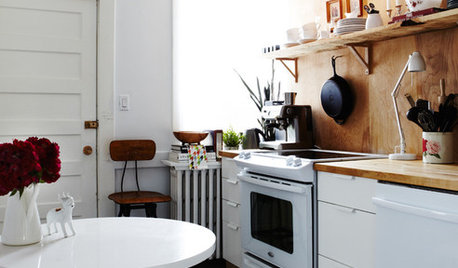
HOUZZ TOURSHouzz Tour: Clean, Chic and Cost-Effective
Canadian designer Jennifer Hannotte designs her Edwardian home in a modern style that can grow with her family
Full Story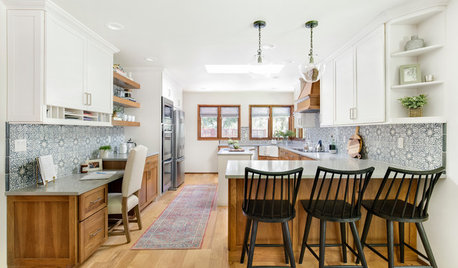
KITCHEN DESIGN6 Elements of an Effective Kitchen Office
Create a successful mini workspace with these features in mind
Full Story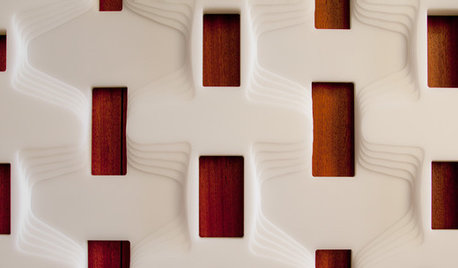
REMODELING GUIDESInterior Materials Get Special Effects Treatment
For truly standout home interiors, forgo painted drywall in favor of unusual materials and eye-catching designs like these
Full Story
mightyanvil