roof/ceiling insulation in south - new construction
Cyndy
5 years ago
Featured Answer
Sort by:Oldest
Comments (18)
David Cary
5 years agoCyndy
5 years agoRelated Discussions
Insulation considerations for new construction
Comments (8)Hi Solarguy, Thanks for the chock full of info. For the ornl.gov site, I'm not getting the same numbers. Did you assume polyurethane or something else for insulation? Either way, I think you are right that I should aim for a much higher R-value. Owens Corning recommends R7 rigid foam exterior sheathing and R21 for the wall cavities for R28 total. Right now for walls, I have cedar shingle siding, standard OSB sheathing, R-15 fiberglass batts, 6mm vapor barrier, then finally drywall. The air infiltration was below min standards so they added a heated air-exchange. I like the idea stopping air before it enters the wall cavity, so rigid foam sheathing and foam spraying the cavity perimeter makes more sense. I mean, I'm stopping the air from passing thru the houses interior, but I'm sure I've got air movement in the wall cavity which kills my fiberglass R-value. Gary Reif, If you could provide a link for the 8.5" wall contruction you are mentioning, that would be great. This along with solargary's insulation upgrade calculator should arm me with enough info to calculate various ROI. Thanks guys....See Morenew roof insulation ventilation dilemma
Comments (7)We wanted to renovate the 1/2 story of our bungalow to make a master suite. We also badly needed a new roof and it had 4 layers of old shingles on it. So, we gutted the upstairs and the first stage was a new roof. Off came four layers of shingles. The oldest were shakes, so there were boards they were nailed to, but no sheathing. We wanted a cold deck roof (because DH suffered a bad fall shoveling the da*n thing a few years back - crushing his heel!). The contractor installed sheathing that was foam backed OSB; it wasn't sandwich board - it was OSB board on one side & foam on the other (probably because we had those old nailer boards across the joists). Anyway, the new 40 year shingles went on over the foam backed OSB. That was about 4 years ago. It was really expensive. I swear we have the most expensive roof in town on our little house! Fast forward to last year... still working on the house. Now, it's time to finish the upstairs and we have to insulate between the roof joists in order to get ready to hang the drywall. The roof doesn't have vents, so we can't do fiberglass; the general contractor recommened spray foam, so that's what we did last spring. That was another $6-7,000. The spray foam added another R38 to the two inches of foam under the sheathing, so now we have something like an R52 roof. Let me tell you though, the upstairs does not get hot in the summer like it used to, we have a true cold deck roof - nary an icicle and no ice dams - and it stays cozy in the winter with very little help from a gas fireplace we added to the upstairs as the only heat source. The upshot is we are very happy with the outcome as to energy efficiency, indoor climate control, and roof/snow management. Was it expensive? YES. Hope this helps....See MoreNew home construction - Roof/Ceiling
Comments (9)1/8" inch is the standard recommended gap by the APA for OSB unless the panel manufacturer recommends a different gap. However, there appear to be sheathing clips on your roof, which can work with a larger gap and are used to strengthen the roof when panel edges are unsupported, i.e., do not land on the roofing structure. Some jurisdictions may require these clips; they are a good idea in any case. You might want to check that the gap doesn't exceed the maximum for the clips being used and that the clips are correctly spaced. If you have a proper framing inspection in your jurisdiction, that's something the inspector should be knowledgeable about....See MoreLow profile LED lights for new construction with foam insulation?
Comments (2)There are many options that will work (junction box, led disk with ceiling clips, wrapped ICAT). I guess what I was asking was what makes the most sense. Rafters are 5.5"....See MorePPF.
5 years agoSpringtime Builders
5 years agolast modified: 5 years agoSam Goh
5 years agocpartist
5 years agoDavid Cary
5 years agoCyndy
5 years agoCyndy
5 years agoCyndy
5 years agoJeffrey R. Grenz, General Contractor
5 years agoSam Goh
5 years agoSpringtime Builders
5 years agolast modified: 5 years agoCharles Ross Homes
5 years agoSpringtime Builders
5 years agolast modified: 5 years agoCharles Ross Homes
5 years agoSpringtime Builders
5 years agolast modified: 5 years ago
Related Stories
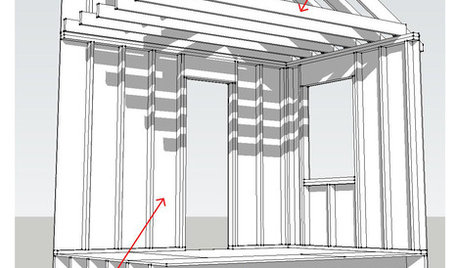
KNOW YOUR HOUSEKnow Your House: Components of a Roof
Don't get held up by confusion over trusses, rafters and purlins. Learn about a roof's features and their purposes here
Full Story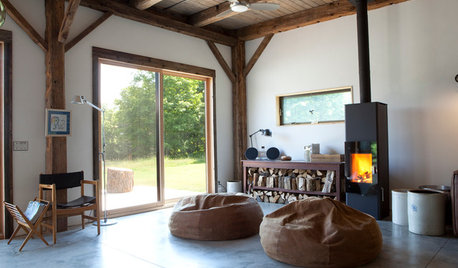
GREEN BUILDINGInsulation Basics: Heat, R-Value and the Building Envelope
Learn how heat moves through a home and the materials that can stop it, to make sure your insulation is as effective as you think
Full Story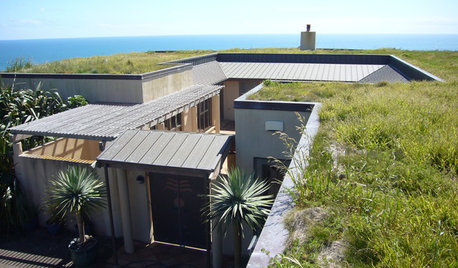
GREEN BUILDINGLiving Roofs Put Down Roots
No longer solely the domain of hippies — or hobbits — a green roof can be a hardworking partner in making your house sustainable
Full Story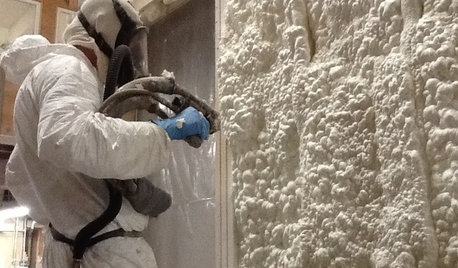
MATERIALSInsulation Basics: What to Know About Spray Foam
Learn what exactly spray foam is, the pros and cons of using it and why you shouldn’t mess around with installation
Full Story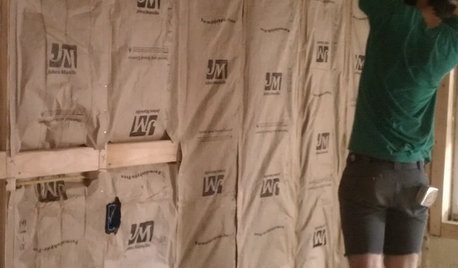
REMODELING GUIDESCool Your House (and Costs) With the Right Insulation
Insulation offers one of the best paybacks on your investment in your house. Here are some types to discuss with your contractor
Full Story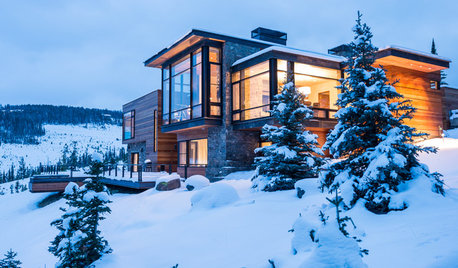
ARCHITECTUREHave Your Flat Roof and Your Snow Too
Laboring under the delusion that flat roofs are leaky, expensive and a pain to maintain? Find out the truth here
Full Story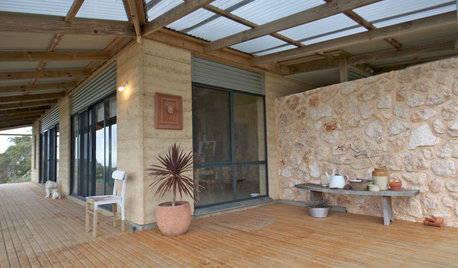
HOUZZ TOURSMy Houzz: A South Australia Home Comes Down to Earth
Rammed-earth walls embrace nature, stand up to harsh coastal conditions and create an indoor-outdoor connection for this artist's home
Full Story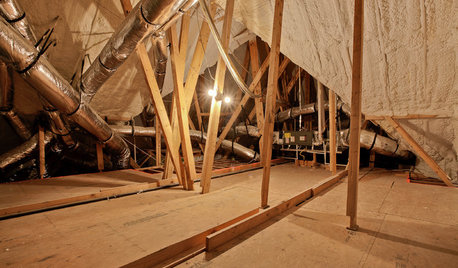
GREEN BUILDINGEcofriendly Cool: Insulate With Wool, Cork, Old Denim and More
Learn about the pros and cons of healthier alternatives to fiberglass and foam, and when to consider an insulation switch
Full Story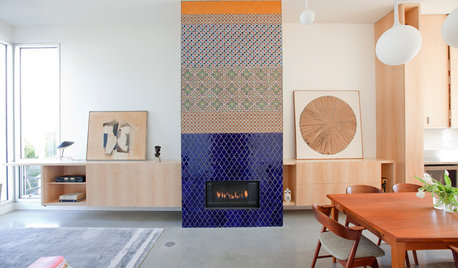
HOUZZ TOURSHouzz Tour: Innovative Home Reunites Generations Under One Roof
Parents build a bright and sunny modern house where they can age in place alongside their 3 grown children and significant others
Full Story
riverrat1