I am finally building my house. Attic question.
liv2tell
7 years ago
last modified: 7 years ago
Featured Answer
Sort by:Oldest
Comments (58)
Apolonia3
7 years agololauren
7 years agoRelated Discussions
I am ready to document my build...
Comments (56)OK, The pavers are done, and salt is in the pool. I am putting stone to match the house on all of the retaining walls myself in the next few weeks, then I will cap them off with bricks that match the house. Finish grading and clean up is tomorrow. I then have plenty of planters (4) to landscape too. Overall A&S was fine to work with. Like I was told in the beginning, their on site management could be better. Sometimes it seems they would rather have the subs do something wrong, and then fix it later, than to just keep a project manager at the site more often. But, they did respond quickly to all of my requests and changes. And I am a picky person when it comes to projects like these. Anyhow, I appreciate all of the ideas, suggestions, and comments from you guys and gals. Here are some photos. I will post others after the stone is on the walls and the landscaping is in. (BTW, the pavers are Dublin's Potomac 3 peice, and the water is very dirty from all of the paver dust... it actually is a much crisper blue than is appearing here)...See MoreBuilding a sunroom on the back of my house question
Comments (4)Im working on a project where concrete was poured over an existing sloped slab in the garage to get a level base,(converting the garage into living space). The concrete contractor does not like to go less than 1-1/2" of new over old. He also only uses fibered reinforced concrete which doesn't finish as well,(if you are having stained concrete floors for example), but is structurally sounder. He also drilled holes in the existing slab about every 24" or so to allow the new to "bite" into the old. With 6" of new concrete, another avenue that might be overkill but would give you good peace of mind would be to drill in and epoxy rebar that sticks up about 3 " all around in the old slab and attach wire mesh to the rebar. You also want to drill in rebar into the sides of the existing slab where your footers will butt up to them. Drill in and epoxy rebar about every 24" horizontally and leave about 6" or so of rebar out for the new concrete in the footers to grab onto. Then run rebar all along the perimeter tying into the horizontal peices,(laying on top), that are protruding out from the old slab. The rebar along the perimeter will be centerd in the footing the length of the footers laying on top of and tied into the horizontal pieces epoxied into the existing slab. Hope this helps!...See MoreThoughts on this Don Gardner House I am planning to build?
Comments (31)Dining rooms really do require some thought when there's symmetry involved as in your plan. The lighting fixture is usually centered over the table, so you must know where it will go early on. It is also usually centered on the window when the window is located where yours is, and also on the Foyer doorway when it looks like yours. Will you have a buffet and/or china cabinet? If either is on the long wall opposite the wide Foyer doorway, the window might be shifted to the left, and you would have to consider how this would affect the space left for seating around the table, as well as the front elevation. If neither is on this wall, you'd want to have a focal point from the Foyer doorway--a group of pictures, a large painting, etc. on the long wall. If either is on the wall to the left of the Butler's Pantry, you would also have to consider how much space would be left for seating, and possible take some space from the Pantry and B. Pantry. If you did the latter, I'd get rid of the B. Pantry by turning the cabinet to face the hall, and make it a "To Go" setup--keys, charging station, mail sorting, travel stuff, etc. Or extend the Mudroom. It also might change how wide you want the opening to the Foyer on the "north" end. The Pantry can be any depth down to a finished 9" inside, and could be quite wide with 2 or 3 doors to make everything easily accessible. I saw one like this in a model home, and liked it so much that I tried unsuccessfully to work it into my plan. To have a place for some larger items, I think a pantry with about a 15" finished interior would be sufficient, but it depends on what YOU plan to put in there besides cans & normal sized grocery items. I hope others can add to this from their DR experiences. Anne...See MoreBuilding my own house! Will need advice as I go!
Comments (92)My construction is very similar to our main office at work. I don't have a dog in this fight, so I really don't give a crap whether your house lives like your office or like my home. However, I can tell you that we have a couple of commercial buildings just like this on the farm and your building looks similar to my father's warehouse which has an office. Those are not homes. I don't care how it is usually done, I care about the marginal cost of doing it better and, in fact, the marginal cost of doing it better is low enough that not doing it better is shortsighted and wasteful. There is little point in trying to build those to the same standards as my home, the amount of air passing in and out through openings necessary for business make many of those things moot. However, when you attempt to tighten those openings up you don't simply get a tighter house, you get a moldy and/or uncomfortable space. Is it livable? Sure it is, people make due with a lot worse. Is it optimal? No! Is it even suboptimal in any practical way? No! Are you going to believe me or even use the device you are typing your response on to actually investigate whether or not good enough is really good enough? Probably not. I wish you all the best. Enjoy....See MoreUser
7 years agolast modified: 7 years agoUser
7 years agolast modified: 7 years agoVirgil Carter Fine Art
7 years agoworthy
7 years agolast modified: 7 years agoliv2tell
7 years agoliv2tell
7 years agolast modified: 7 years agocpartist
7 years agoSammy
7 years agolast modified: 7 years agoVirgil Carter Fine Art
7 years agoliv2tell
7 years agoliv2tell
7 years agoworthy
7 years agolast modified: 7 years agoVirgil Carter Fine Art
7 years agoliv2tell
7 years agoliv2tell
7 years agoUser
7 years agolast modified: 7 years agoworthy
7 years agoVirgil Carter Fine Art
7 years agoworthy
7 years agolast modified: 7 years agoliv2tell
7 years agoliv2tell
7 years agoUser
7 years agolast modified: 7 years agoliv2tell
7 years agoVirgil Carter Fine Art
7 years agocpartist
7 years agoworthy
7 years agolast modified: 7 years agoSammy
7 years agolast modified: 7 years agoworthy
7 years agolast modified: 7 years agoUser
7 years agolast modified: 7 years agoSpringtime Builders
7 years agolast modified: 7 years agoliv2tell
7 years agolast modified: 7 years agoUser
7 years agoUser
7 years agolast modified: 7 years agoVirgil Carter Fine Art
7 years agoUser
7 years agolast modified: 7 years agoliv2tell
7 years agoUser
7 years agolast modified: 7 years agoUser
7 years agolast modified: 7 years agoUser
7 years agolast modified: 7 years agoUser
7 years agolast modified: 7 years agoUser
7 years agolast modified: 7 years agoUser
7 years agolast modified: 7 years agoUser
7 years ago
Related Stories
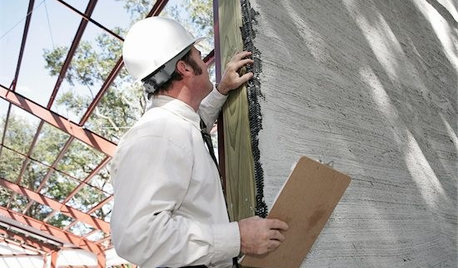
MOVINGHiring a Home Inspector? Ask These 10 Questions
How to make sure the pro who performs your home inspection is properly qualified and insured, so you can protect your big investment
Full Story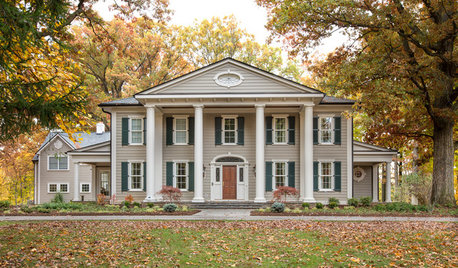
SELLING YOUR HOUSE15 Questions to Ask When Interviewing a Real Estate Agent
Here’s what you should find out before selecting an agent to sell your home
Full Story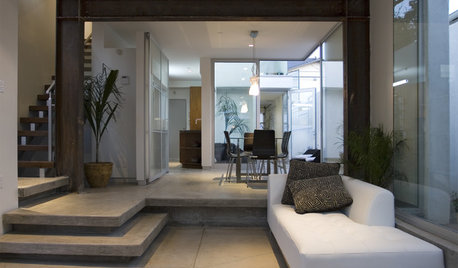
GREEN BUILDINGConsidering Concrete Floors? 3 Green-Minded Questions to Ask
Learn what’s in your concrete and about sustainability to make a healthy choice for your home and the earth
Full Story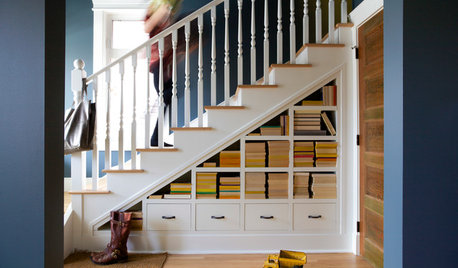
ORGANIZINGPre-Storage Checklist: 10 Questions to Ask Yourself Before You Store
Wait, stop. Do you really need to keep that item you’re about to put into storage?
Full Story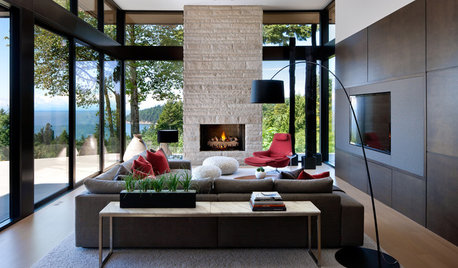
WORKING WITH PROS9 Questions to Ask a Home Remodeler Before You Meet
Save time and effort by ruling out deal breakers with your contractor before an in-person session
Full Story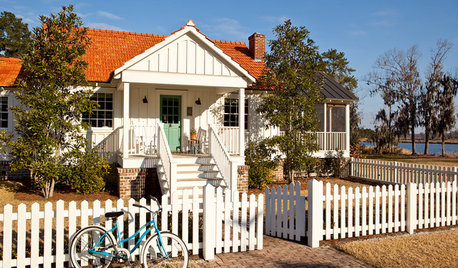
REMODELING GUIDESConsidering a Fixer-Upper? 15 Questions to Ask First
Learn about the hidden costs and treasures of older homes to avoid budget surprises and accidentally tossing valuable features
Full Story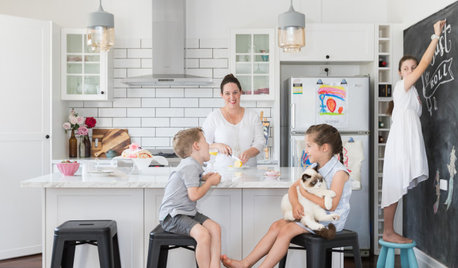
FEEL-GOOD HOMEThe Question That Can Make You Love Your Home More
Change your relationship with your house for the better by focusing on the answer to something designers often ask
Full Story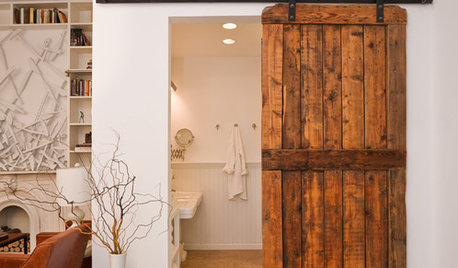
DOORS5 Questions to Ask Before Installing a Barn Door
Find out whether that barn door you love is the right solution for your space
Full Story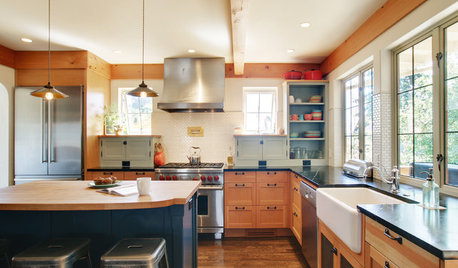
MOST POPULAR8 Questions to Ask Yourself Before Meeting With Your Designer
Thinking in advance about how you use your space will get your first design consultation off to its best start
Full Story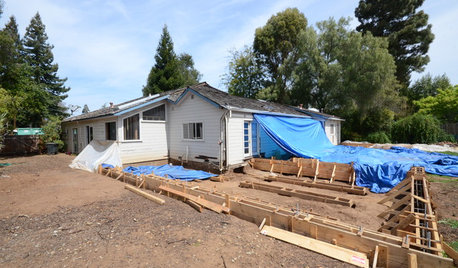
REMODELING GUIDESSurvive Your Home Remodel: 11 Must-Ask Questions
Plan ahead to keep minor hassles from turning into major headaches during an extensive renovation
Full Story
Springtime Builders