Babushka Cat's Finished Kitchen!
babushka_cat
7 years ago
Featured Answer
Sort by:Oldest
Comments (34)
Karen Viscito Interiors
7 years agomama goose_gw zn6OH
7 years agolast modified: 7 years agoRelated Discussions
3 Year Old Cat Female Cat Marking_What to do-long
Comments (28)I see there is interest in this so I'll link to my animal communicator's website. The communicator, Gayle Nastazi, has always been very helpful to me. I have used her services with many of my cats in various situations; from dire emergencies (missing animal- found after 3 weeks!), to behavioral issues, to intergration and rescue issues with feral and abandonned cats that come into my care. I always learn something from every session. Although I know the whole idea strikes some people as pretty far-fetched (and that's OK), I feel comfortable saying that it has worked very effectively for me, and that I think it makes resolution of some difficult issues much easier. One thing I can say for certain is that Gayle is completely legitimate. I have met her in person. I also have no financial interest in this referral - just a hope that my suggestion might be useful. Click on the clink below and look for the Animal Communication link at the top left of the page. Carry on from there if you are interested. RE: Various Animal pee cleaners/destinkes - I think many (most?) employ some kind of enzyme. My conclusion after using all of them is that after the bottles are opened and partly used that it's possible that exposure to air in the emptying bottle degrades the enzyme significantly. It always seems to me that they work like gangbusters at first and then less so, particularly if not used up in a short time. Then I try another brand and it seems to work better (even tested side by side), but eventually poops out, too. I have tried Odor-X, Nature's Miracle and Get Serious, along with scads of others. The pattern seems to hold for all, so now I only buy in quarts not gallons, even though it's 'way cheaper in big jugs. I haven't experimented with decanting a gallon into smaller jars and keeping them closed until I've used up the other portions. Also I find it's helpful to vigorously shake the plastic bottle before applying. The idea mentioned by olychik about using rags is v. interesting and I will keep it mind. I hope that my link may be useful to you. Here is a link that might be useful: Link to Gayle Nastazi, Animal Communicator's webpage...See Morecat_mom's finished kitchen (double posted from discussions)
Comments (23)Thank you so much nannymac! We did use a KD to design the kitchen (layout, cab/drawer locations, island/tabletop leg design), and he worked very closely with us to incorporate our "vision" for the space, which we (DH and I and our KD) tweaked along the way as needed or desired. The details were all chosen by us; e.g. the appliances, fixtures, granite, backsplash, cab hardware (even the cherry wood switchplates, which we ordered and then gave him to have the cab manuf stain to match the cabs). Those items (among others) we researched/found on our own. The bathrooms were "all us!" LOL. Of course, we were (and still are) extremely fortunate to have a great tile guy, and tile place(s), and plumber, to help and advise us when necessary, since we were our own GC's for the bathrooms (as well as the kitchen). Our bath/kitchen/hardware showroom salesperson was invaluable (literally) in helping us pick and choose fixtures, for function, price, quality, and style. He knew the look we were trying to create (and the price ranges of the different lines, and our budgetary constraints), and we bounced a lot of ideas off each other....See MoreFor Babushka_cat - finished kitchen?
Comments (2)hi christine- thanks so much for the follow up and enthusiasm for my project! i am close but not yet finished. took me a while to find my backsplash tile. i have found "the one" but of course the one i selected has a 6-7 week lead time and then need to have it installed along with finish electric and breakfast nook furnishings. will be another two months or so but am close! thanks again for the encouragement, much appreciated! GW has been a tremendous resource, i will be sure to post when complete. babushka cat...See MoreBabushka-what kind of screws did u buy for pull
Comments (3)Michelle--even in my small town, there are two large hardware stores with thousands of screws that should stock anything you need. It should be easy for a GC to find the correct screws for your pulls. I had to do this with some Hafele pulls on the MBR built-ins to save some time for my cab maker. He gave me the screws that came with the pulls and told me what needed to be different about them to make them work. I took them to the local hardware, handed the screw dept guy the sack, told him what I needed, and two minutes later I walked out with exactly the right product. Easy peasy. I wouldn't worry about finding someone to tell you which screw they used. Your cab maker will know the thickness of your specific drawer fronts and can offer guidance. Good luck!...See Morenini804
7 years agoUser
7 years agoblfenton
7 years agoBunny
7 years agotea4all
7 years agobeachem
7 years agorebunky
7 years agolast modified: 7 years agocat_mom
7 years agodesertsteph
7 years agopractigal
7 years agomgmum
7 years agolam702
7 years agobarncatz
7 years agolast modified: 7 years agoWendy
7 years agoknancy1947
7 years agocaligirl5
7 years agoamykath
7 years agoediblekitchen
7 years agoR G MILLER (YBC)
7 years agoUser
7 years agocpartist
7 years agoJoseph Corlett, LLC
7 years agomabeldingeldine
7 years agoenduring
7 years agoromy718
7 years agobabushka_cat
7 years agobabushka_cat
7 years agoUser
7 years agolast modified: 7 years agocpartist
7 years agolast modified: 7 years agopowermuffin
7 years agobeachem
7 years agolast modified: 7 years ago
Related Stories
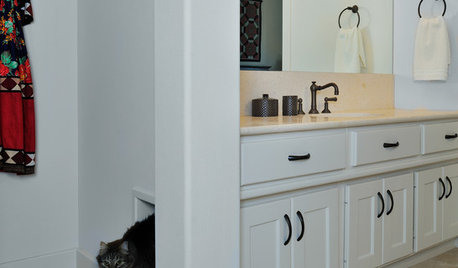
PETSSo You Want to Get a Cat
If you're a cat lover, the joys outweigh any other issue. If you haven't lived with one yet, here are a few things to know
Full Story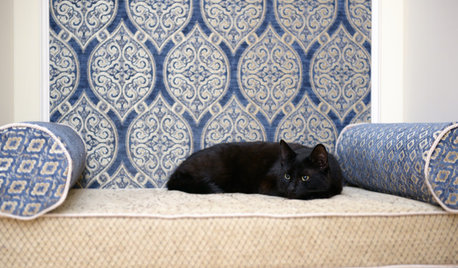
PETS10 Tips for Keeping Indoor Cats Healthy and Happy
It's National Cat Day: Ask not what your cat can do for you (because it will ignore you) but what you can do for your cat
Full Story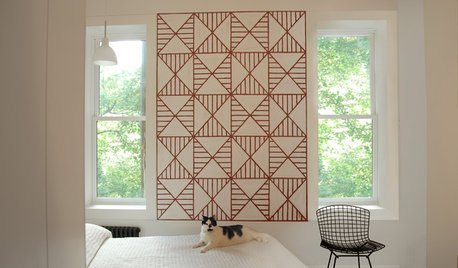
PETSHouzz Call: Send in the Design Cats
Post your best photo of your cat at home, in the garden or with you in your studio. It could be published in a featured ideabook
Full Story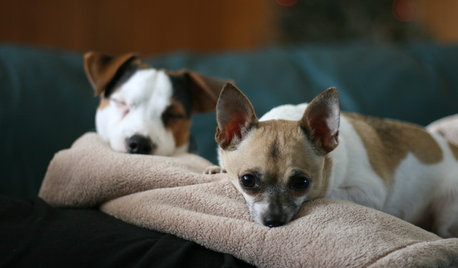
PETSHouzz Pets Survey: Who Rules the House — Dogs or Cats?
New data shows that pets make people happy, and pet owners love spending big to return the favor
Full Story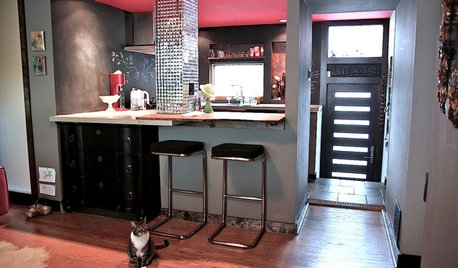
HOUZZ TOURSHouzz Tour: For the Love of a Cat in Philadelphia
Pet-friendly features integrated into a mod, eclectic and colorful home mean everyone in the family is happy
Full Story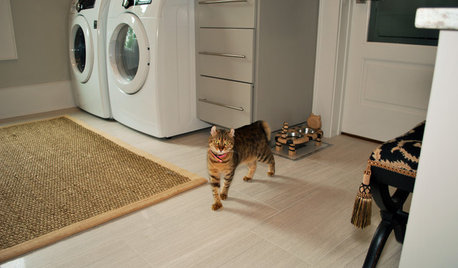
THE HARDWORKING HOMEA Laundry Makes Room for a Diva Cat
A South Carolina laundry room was designed to be sophisticated and functional, but when a kitten arrived, whimsy emerged
Full Story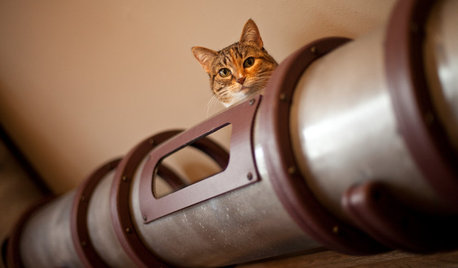
FUN HOUZZGeek Lab: How to Build a Steampunk Cat Transit System
Give your kitty another avenue for fun with a tubular walkway system that lets him go his own way
Full Story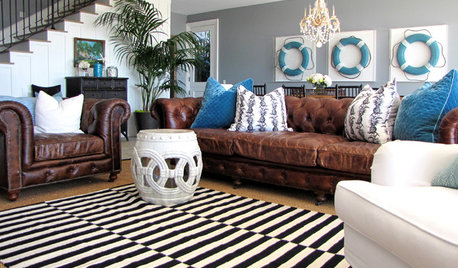
PETS5 Finishes Pets and Kids Can’t Destroy — and 5 to Avoid
Save your sanity and your decorating budget by choosing materials and surfaces that can stand up to abuse
Full Story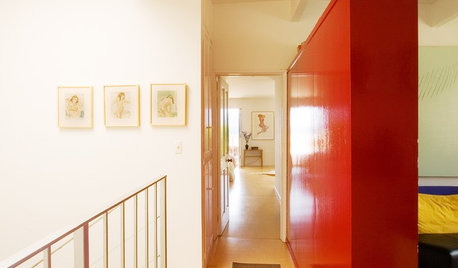
WALL TREATMENTSPick the Right Paint Finish to Fit Your Style
The question of finish may be as crucial as color. See which of these 9 varieties suits your space — and budget
Full Story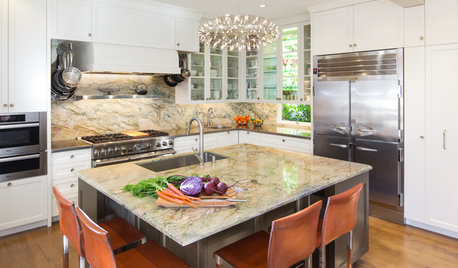
KITCHEN DESIGNKitchen of the Week: Elegant Updates for a Serious Cook
High-end appliances and finishes, and a more open layout, give a home chef in California everything she needs
Full StorySponsored
Your Custom Bath Designers & Remodelers in Columbus I 10X Best Houzz
cluelessincolorado