Let's talk housewrap
josh02_2001
8 years ago
Featured Answer
Sort by:Oldest
Comments (50)
worthy
8 years agoRelated Discussions
Let’s talk blue light computer glasses
Comments (8)I recently (this week) saw a news segment about them.Of course I can’t remember exactly what news outlet. I did find the following which is what the report said. “ The American Academy of Ophthalmology says you don’t need them and has gone on record as not recommending any kind of special eyewear for computer users. The organization says blue light from digital devices does not lead to eye disease and doesn’t even cause eyestrain. The problems people complain about are simply caused by overuse of digital devices, it says. “The symptoms of digital eye strain are linked to how we use our digital devices, not the blue light coming out of them,” the AAO says.” https://www.webmd.com/lung/news/20210115/do-blue-light-glasses-work...See MoreLet’s just keep talking about wedding outfits
Comments (73)Lyban, I am not surprised you’re confused because I’ve been talking about multiple weddings! The earrings from an earlier post were for this dress, my MOG dress for early spring. No necklace, because there is a small ”diamond” bedazzlement already on the dress. THIS navy dress is what I am wearing to a wedding in Sept. And I ordered and received these navy shoes, and I like them so I’m wearing them. And I already have the exact shoes in silver to wear with the fuschia dress next spring. They are very comfortable. I like the navy dress so much, I may wear it for the rehearsal dinner for DS’ wedding. The lace pattern is all heart shapes, which verges a bit on maybe-too-cutesy but it’s fairly subtle....See MoreLet’s talk about funeral homes!
Comments (47)My mother had purchased her interment site decades ago - in her hometown, where she hadn't lived for the decades since. She had also picked out a dress to be buried in, and had shown it to me several times in the years before her final illness. She was in a nursing home in my town, 115 miles away, with hospice. The nursing home (or hospice, I don't recall which) arranged for her remains to be picked up by a local mortuary after death was declared. I arranged the funeral with the funeral home in her hometown, that had been used by my family many times. They arranged to have the body transported to them, handled all of the paperwork (including obtaining the death certificate from my county), and placed the obit that I wrote in the local paper. 3 of my 4 siblings, my aunt and her best friend, and 2 of 5 my nieces came to the small service that we had in a parlor of the funeral home. There was no one else who knew or were friends with her (and I had no friends that I had remained in contact with) left in town. My niece's husband (they lived locally) arranged for the chaplain from his work to give a little homily and lead prayer; I found a musician to play 3-4 of her favorite hymns on guitar. Then all we went to the interment at the cemetery. One of my SILs arranged with someone she knew to prepare and serve a casual lunch in a facility at the cemetery for us. BTW, that was the only family member who did anything - the others never even offered - to arrange or help pay for it all. Mom didn't have any insurance benefit or funds left to help pay. ETA: I did all this really out of respect for my elderly aunt - that it pleased my sister and 2 of her daughters was nice but really not a consideration. My brothers wouldn't have minded either way, but I was glad that the oldest drove up from Tennessee - I hadn't seen him in many years, and probably never will again - I was 7 when he left home at the age of 18 and we were never close as adults. At the time it was rather a stretch for my finances. So, I did negotiate with the funeral home about the charges; in fact, I declined their caskets and found a company that sold and delivered lovely caskets in Cincinnati at a much lower cost....See MoreLet’s talk “appropriate”………
Comments (164)Oh yeah I don’t think I had a manicure or pedicure until I was probably 35! I am horrible at shaping nails and my cuticles grow huge, so a manicure is great. I don’t have super long nails, and I usually just do regular polish though I will do gel manicure for travel sometimes. I love the foot massge with pedicures. I’ve asked DH to join me for a pedicure, but he’s not interested nor is MIL in joining me for either so I just go alone. No tattoos. We are probably the only un-tatooed people at any rock show we go to LOL. I would definitely get something of all my cats if I did. I’ve seen some super cool ones of cats, either line draws or something really whimsical or realistic....See Morejosh02_2001
8 years agoUser
8 years agolast modified: 8 years agojosh02_2001
8 years agolast modified: 8 years agoUser
8 years agolast modified: 8 years agoSpringtime Builders
8 years agolast modified: 8 years agoenergy_rater_la
8 years agoUser
8 years agolast modified: 8 years agoenergy_rater_la
8 years agojosh02_2001
8 years agoCharles Ross Homes
8 years agoUser
8 years agolast modified: 8 years agoCharles Ross Homes
8 years agoUser
8 years agolast modified: 8 years agojust_janni
8 years agoUser
8 years agolast modified: 8 years agobailey4980
7 years agolast modified: 7 years agobailey4980
7 years agobailey4980
7 years agobailey4980
7 years agolast modified: 7 years agoagagent3
7 years agoCharles Ross Homes
7 years agobailey4980
7 years agolast modified: 7 years agobailey4980
7 years agoworthy
7 years agolast modified: 7 years agoenergy_rater_la
7 years agolast modified: 7 years agobailey4980
7 years agoworthy
7 years agolast modified: 7 years agobailey4980
7 years agoUser
7 years agolast modified: 7 years agobailey4980
7 years agolast modified: 7 years agoSpringtime Builders
7 years agolast modified: 7 years agoUser
7 years agolast modified: 7 years agobailey4980
7 years agoSpringtime Builders
7 years agolast modified: 7 years agobailey4980
7 years agolast modified: 7 years agoSpringtime Builders
7 years agolast modified: 7 years agobailey4980
7 years agolast modified: 7 years agobailey4980
7 years agolast modified: 7 years agobailey4980
7 years agolast modified: 7 years agoUser
7 years agolast modified: 7 years agoworthy
7 years agolast modified: 7 years agobailey4980
7 years agoUser
7 years agolast modified: 7 years agoUser
7 years agolast modified: 7 years agobailey4980
7 years agoworthy
7 years agolast modified: 7 years agoUser
7 years agolast modified: 7 years agoenergy_rater_la
7 years ago
Related Stories
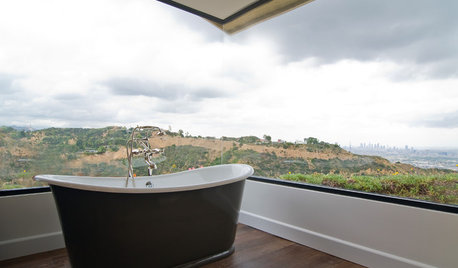
PRODUCT PICKSGuest Picks: Let’s Talk Tubs
Find just the right bathtub no matter how you like to soak
Full Story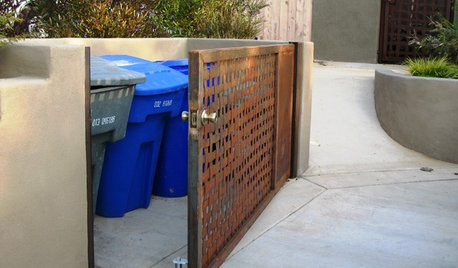
GARDENING AND LANDSCAPINGLet's Talk Trash Bins
No one gazes fondly on garbage cans. Keep your street cred intact and your bins under wraps with these camouflage solutions
Full Story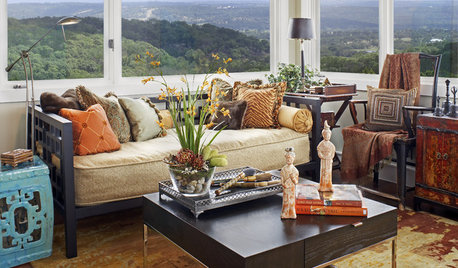
FURNITUREExpert Talk: Dreaming of a Daybed
Whatever color, pattern or style flits through your fancy, today's daybeds let you have it — and practicality too
Full Story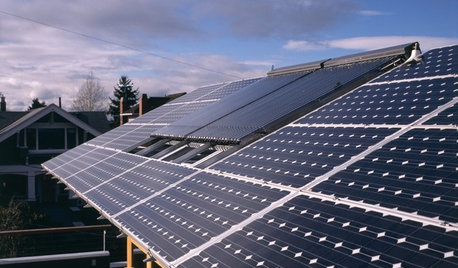
GREEN BUILDINGLet’s Clear Up Some Confusion About Solar Panels
Different panel types do different things. If you want solar energy for your home, get the basics here first
Full Story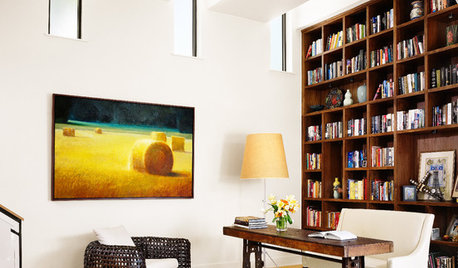
FURNITUREDesign Talk: What is a Settee?
See This Elegant Seating Solution in Dining Room, Office, Entry and Bedroom
Full Story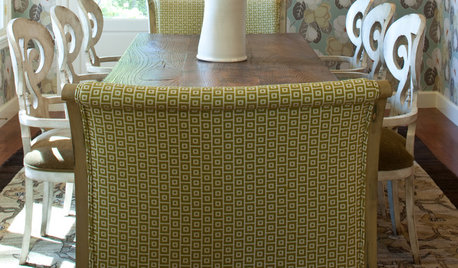
DINING ROOMSExpert Talk: Treat the Eyes to Dining Room Wallpaper
For a visual feast and plentiful servings of style in the dining room, pro designers show how wallpaper fits the bill
Full Story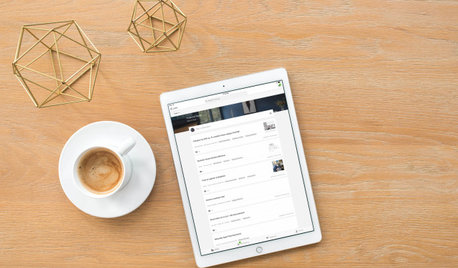
REMODELING GUIDESHave a Design Dilemma? Talk Amongst Yourselves
Solve challenges by getting feedback from Houzz’s community of design lovers and professionals. Here’s how
Full Story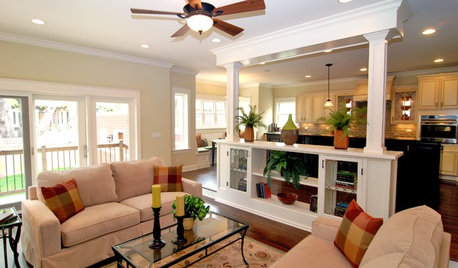
REMODELING GUIDESExpert Talk: Wall Dividers Pull Rooms Together
Open layouts are popular, but these designers explain how a little division can sometimes finish the look of a room the way nothing else can
Full Story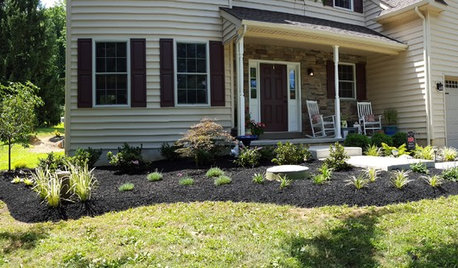
LIFEIf You Could Talk to Your House, What Would You Say?
‘Pull yourself together’ or ‘thank you for transforming my life’? Notes to homes around the country hit us where we live
Full Story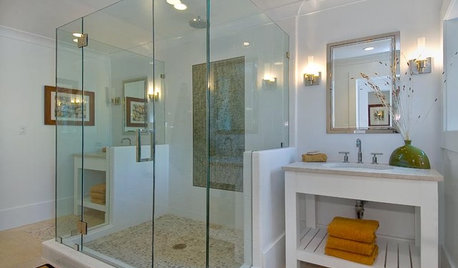
BATHROOM DESIGNExpert Talk: Frameless Showers Get Show of Support
Professional designers explain how frameless shower doors boosted the look or function of 12 bathrooms
Full Story
User