Insulating the outside of a house for air infiltration/R-values.
cissado
18 years ago
Related Stories
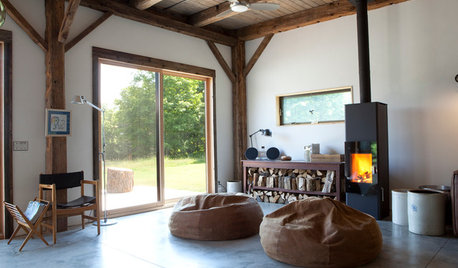
GREEN BUILDINGInsulation Basics: Heat, R-Value and the Building Envelope
Learn how heat moves through a home and the materials that can stop it, to make sure your insulation is as effective as you think
Full Story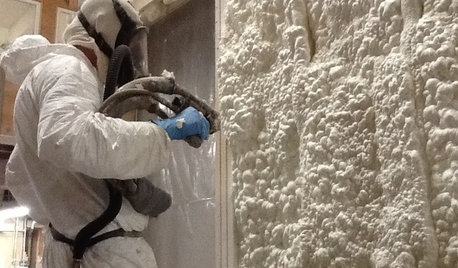
MATERIALSInsulation Basics: What to Know About Spray Foam
Learn what exactly spray foam is, the pros and cons of using it and why you shouldn’t mess around with installation
Full Story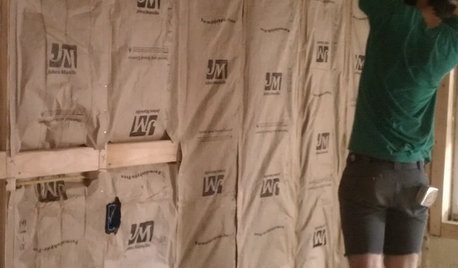
REMODELING GUIDESCool Your House (and Costs) With the Right Insulation
Insulation offers one of the best paybacks on your investment in your house. Here are some types to discuss with your contractor
Full Story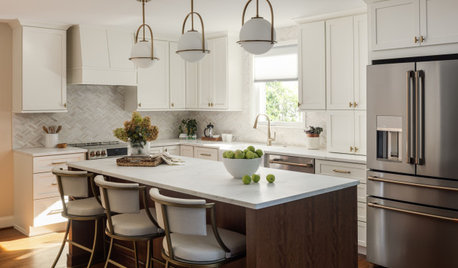
MOST POPULAR5 Remodels That Make Good Resale Value Sense — and 5 That Don’t
Find out which projects offer the best return on your investment dollars
Full Story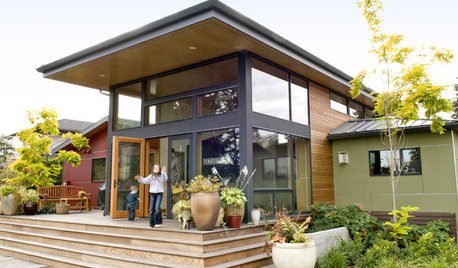
SELLING YOUR HOUSE10 Ways to Boost Your Home's Resale Value
Figure out which renovations will pay off, and you'll have more money in your pocket when that 'Sold' sign is hung
Full Story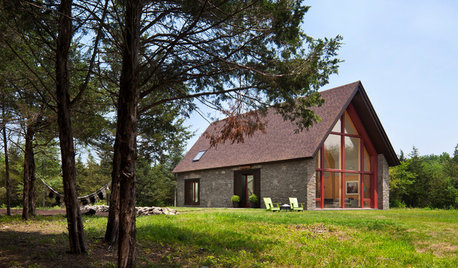
GREEN BUILDINGInsulation Basics: Designing for Temperature Extremes in Any Season
Stay comfy during unpredictable weather — and prevent unexpected bills — by efficiently insulating and shading your home
Full Story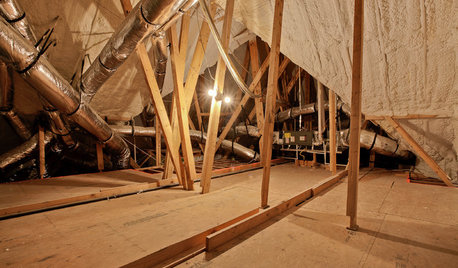
GREEN BUILDINGEcofriendly Cool: Insulate With Wool, Cork, Old Denim and More
Learn about the pros and cons of healthier alternatives to fiberglass and foam, and when to consider an insulation switch
Full Story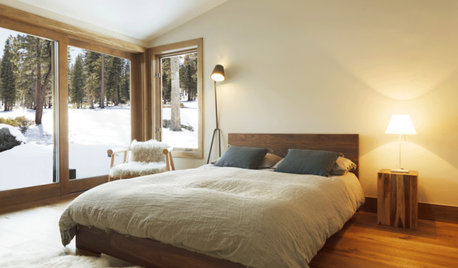
WINDOW TREATMENTSEasy Green: 9 Low-Cost Ways to Insulate Windows and Doors
Block drafts to boost both warmth and energy savings with these inexpensive but effective insulating strategies
Full Story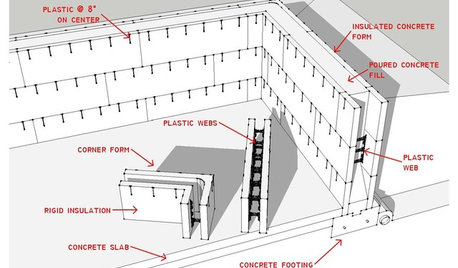
KNOW YOUR HOUSEKnow Your House: The Basics of Insulated Concrete Form Construction
Get peace and quiet inside and energy efficiency all around with this heavy-duty alternative to wood-frame construction
Full Story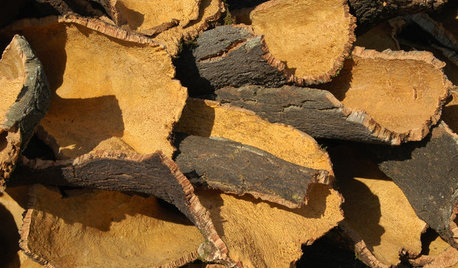
GREEN BUILDINGInsulation Basics: Natural and Recycled Materials
Consider sheep’s wool, denim, cork, cellulose and more for an ecofriendly insulation choice
Full StoryMore Discussions
formulaross
cissadoOriginal Author
Related Discussions
Is there a super-thin, high R-value insulation, not plain rigid?
Q
Trying to fix air infiltration
Q
Air infiltration from storage area
Q
'Air Infiltration', What Consumers Shouold Know First!
Q
glassquilt
sierraeast
cissadoOriginal Author
cissadoOriginal Author
sierraeast
cissadoOriginal Author
beaglebuddy
chaz_oh
cissadoOriginal Author
cissadoOriginal Author
sierraeast
cissadoOriginal Author
chaz_oh
cissadoOriginal Author
chaz_oh
cissadoOriginal Author
cissadoOriginal Author
chaz_oh
beaglebuddy
cissadoOriginal Author
beaglebuddy
cissadoOriginal Author
beaglebuddy
cissadoOriginal Author
beaglebuddy
cissadoOriginal Author
beaglebuddy
cissadoOriginal Author
beaglebuddy
cissadoOriginal Author
beaglebuddy