Homemade apple press
myk1
15 years ago
Related Stories
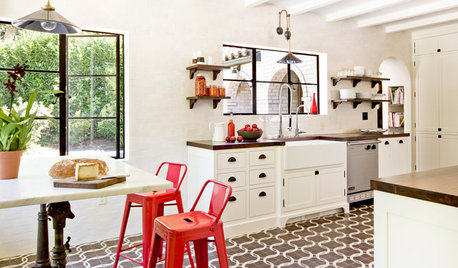
KITCHEN DESIGN16 Scrumptious Eat-In Kitchens and What They Want You to Serve
Whether apple-pie cheerful or champagne sophisticated, these eat-in kitchens offer ideas to salivate over
Full Story
HOLIDAYSA Fresh and Fun Hanukkah Dessert Table and Wrapping Station
Celebrate the Festival of Lights with gelt pouches, homemade snacks and wrapping supplies as pretty as any party decor
Full Story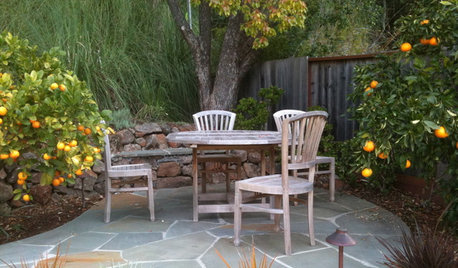
GARDENING AND LANDSCAPINGCrazy for Fruit Trees
Whether a single citrus or a mini apple orchard, even the smallest landscape space can bear deliriously delicious fruit
Full Story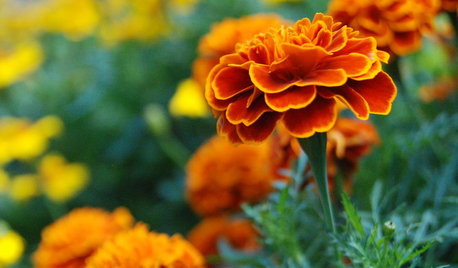
REGIONAL GARDEN GUIDESNortheast Gardener's October Checklist
Go for the gold, get ready for frosts and note your garden combos that looked great
Full Story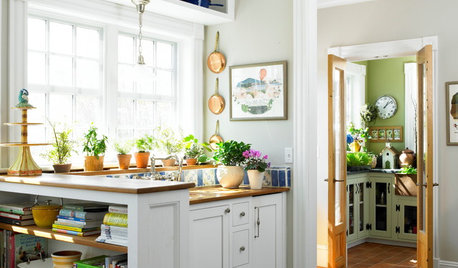
HEALTHY HOME12 Ways to Set Up Your Kitchen for Healthy Eating
Making smart food choices is easier when your kitchen is part of your support team
Full Story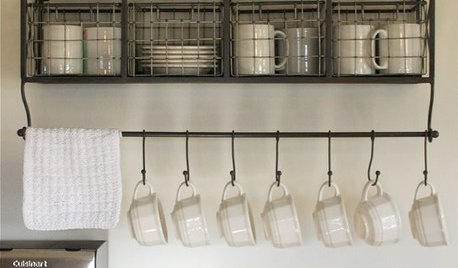
KITCHEN DESIGNHot-Drink Stations Hit the Spot
Beverage bars brimming with cocoa, tea, coffee and all the accoutrements make winter entertaining a delight
Full Story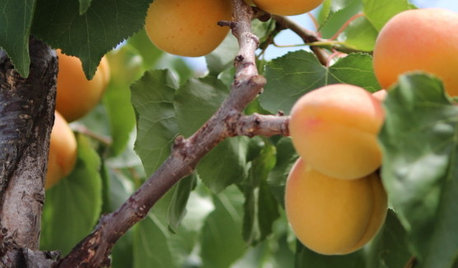
FARM YOUR YARDIf You Have Room for Only One Fruit Tree ...
Juice up a small garden with one of these easier-care or worth-the-effort fruit trees for a mild climate
Full Story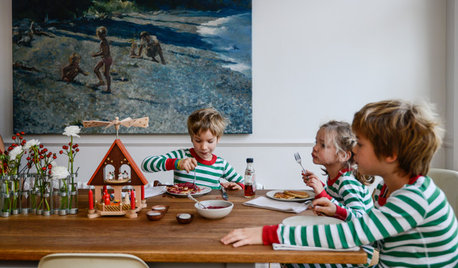
HOLIDAYSHow to Have a Just-Simple-Enough Holiday
Make this the year you say no to holiday stress and yes to joy and meaning
Full Story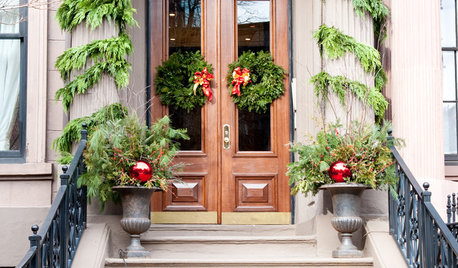
HOLIDAYSShow Us Your Decorated Front Door
Nothing says, ‘Come on in’ like a front door decorated for the holidays. Share pictures of your decorated door in the Comments
Full Story
glib
myk1Original Author
Related Discussions
Hanging basket for pressing flowers and cardboard for pressing
Q
Homemade Apple Pectin Question
Q
Apple press
Q
made apple pie, question about storing homemade whipped cream?
Q
jellyman
myk1Original Author
glib
myk1Original Author
jellyman
Konrad___far_north
myk1Original Author
myk1Original Author
myk1Original Author
jellyman
myk1Original Author
Konrad___far_north
myk1Original Author
hckimball
Konrad___far_north
jellyman
myk1Original Author
olpea
myk1Original Author
Konrad___far_north
olpea
jellyman
Beeone
olpea
jellyman
olpea
myk1Original Author
jellyman
Konrad___far_north
myk1Original Author
olpea
jiminwis
the_gurgler
jellyman
glenn_russell
Konrad___far_north
Konnon6_yahoo_com