Troubles with Kohler Courage 23 HP Twin
dourobob
13 years ago
Related Stories
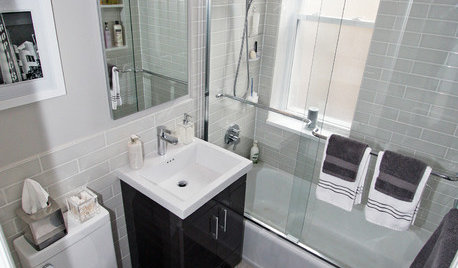
BATHROOM DESIGNWater Damage Spawns a Space-Saving Bathroom Remodel
A game of inches saved this small New York City bathroom from becoming too cramped and limited
Full Story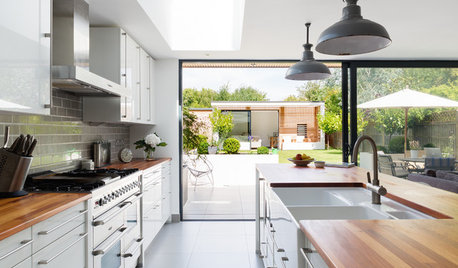
KITCHEN DESIGNA Designer Shares Her Kitchen-Remodel Wish List
As part of a whole-house renovation, she’s making her dream list of kitchen amenities. What are your must-have features?
Full Story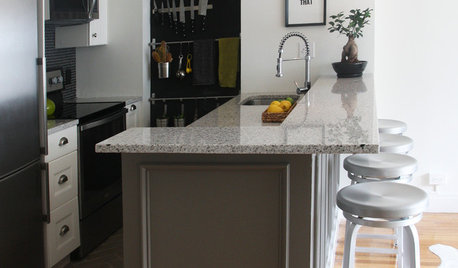
BEFORE AND AFTERSA Boston Kitchen and Bath Go From Dreary to Darling
See how a $25,000 renovation budget gave 2 outdated spaces in a small Massachusetts apartment a brand-new look
Full Story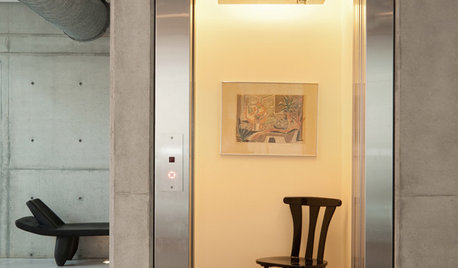
REMODELING GUIDESHome Elevators: A Rising Trend
The increasing popularity of aging in place and universal design are giving home elevators a boost, spurring innovation and lower cost
Full Story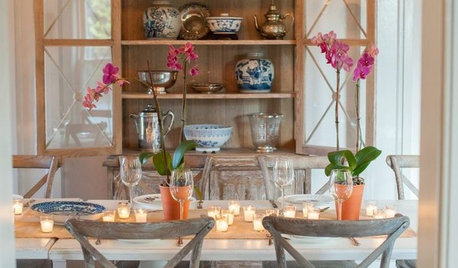
FEEL-GOOD HOMESimple Pleasures: Your Home Is Your Château
Bring a little more beauty and elegance into your daily life with these 8 ideas
Full Story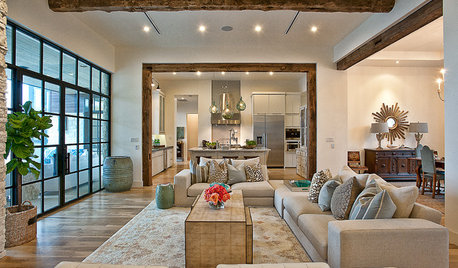
LIVING ROOMSLay Out Your Living Room: Floor Plan Ideas for Rooms Small to Large
Take the guesswork — and backbreaking experimenting — out of furniture arranging with these living room layout concepts
Full Story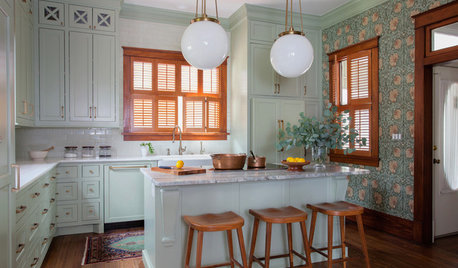
KITCHEN OF THE WEEKKitchen of the Week: Goodbye, Honey Oak — Hello, Minty Green
After more than 30 years, the Kloesels revamped their space to reflect their rural country town and Victorian-style home
Full StoryMore Discussions
buzzard_flats
dourobobOriginal Author
Related Discussions
Kohler 18hp dies after 45 mins
Q
Kohler Command 23hp v twin smoking after service
Q
B&G V-twin vs. Kohler courage ???
Q
Big Time Problems, 25 hp Kohler on Craftsman / Husqvarna/AYP
Q
bushleague
mownie
dourobobOriginal Author
dourobobOriginal Author
mownie
dourobobOriginal Author
dourobobOriginal Author
mownie
dourobobOriginal Author
jdenyer232
mownie
dourobobOriginal Author
mownie
dourobobOriginal Author
mownie
dourobobOriginal Author
shusby
mownie
shusby
mownie
shusby
shusby
mownie
tomplum
shusby
shusby
shusby
shusby
mownie
ewalk
tomplum
shusby
User
ewalk